Rotary Kiln Shell
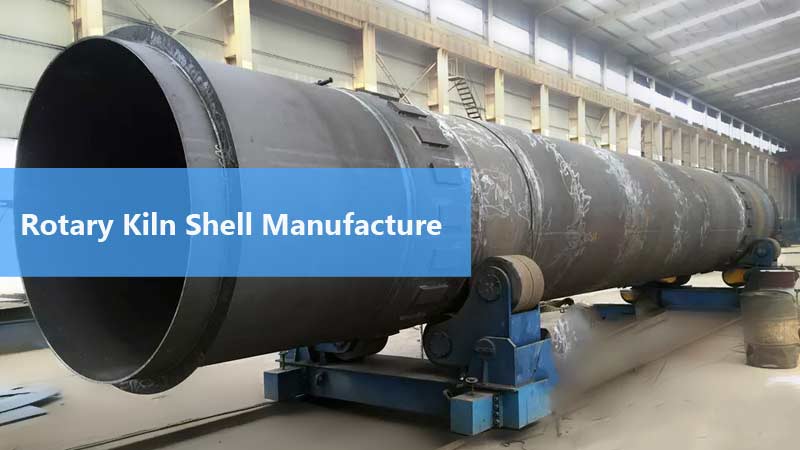
Rotary Kiln Shell Manufacture:
Rotary kiln shell is an important component of rotary kilns, especially large-scale rotary kilns, which have higher requirements for steel plate materials, coiling process, welding process and heat treatment. The rotary kiln shell is made of mild steel plates, and the longitudinal and circumferential gaps of the barrel are automatically welded.
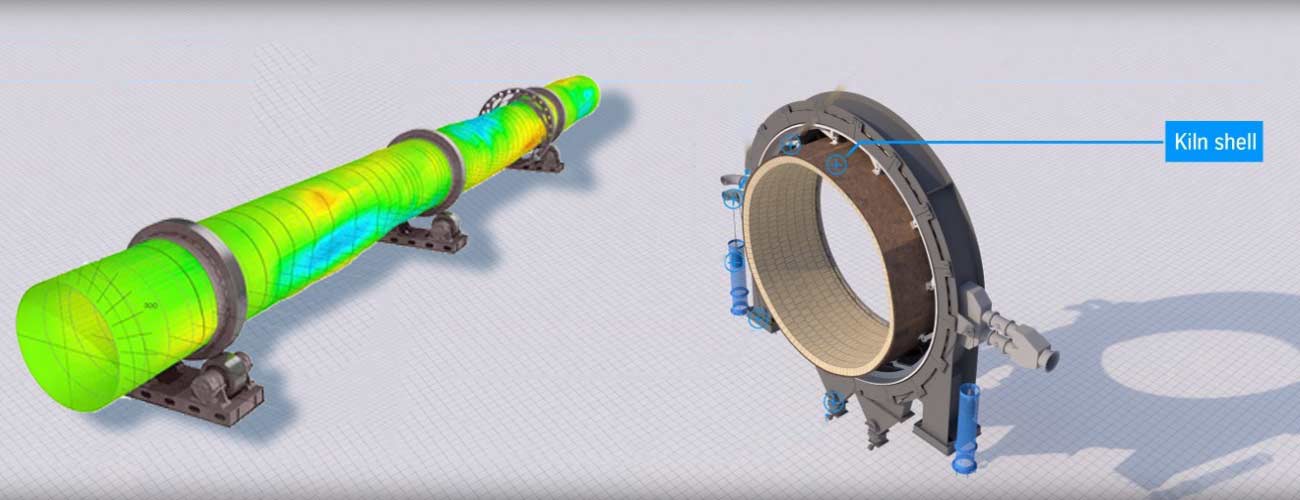
Rotary kiln shell also known as kiln cylinder, is the support and rotating part of rotary kiln equipment. During the long operation, when the rotary kiln shell is in a high temperature state for a long time, the kiln mouth section will deform, manufacturers of rotary kilns generally have corresponding parts casting bases, you can contact after-sales maintenance or manufacturers for rotary kiln shell replacement.
Raw Material for Rotary Kiln Shell
The processing technology of rotary kiln shell affects its quality and working performance. It can be rolled from boiler plate, Q235C plate and other material steel plates, which requires high dimensional accuracy and shape and position tolerance. The processing quality directly affects components properties of strength and tightness.
Customer provide Rotary Kiln Shell Drawing
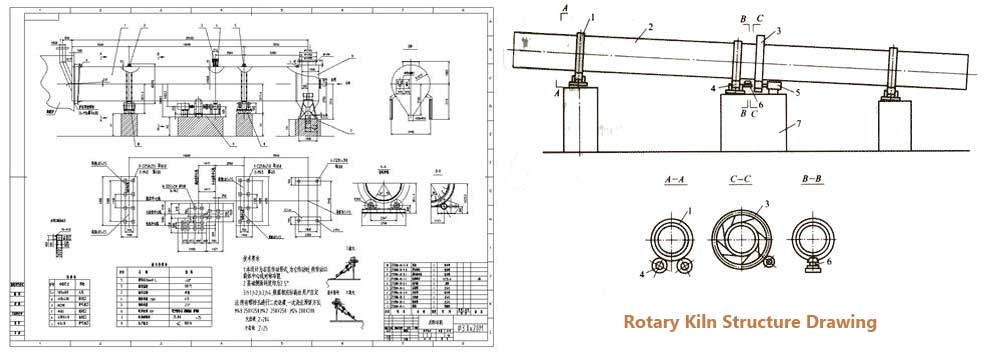
Rotary kiln shell adopts partial forming method. According to the customer requirements of drawings details, the specific production process and welding method of a single-section shell body are formulated. As shell outer circle is not processed, the end face verticality to the center of rotation cannot be directly measured. In the process design, the end face verticality is converted into parallelism and coincidence of the axes of both ends according rotary kiln shell structure.
Rotary Kiln Shell Manufacture Process
After the cylinder body is assembled and welded, post-weld treatment, non-destructive testing, post-weld heat treatment, and pressure test processes to ensure the high-quality cylinder castings production.
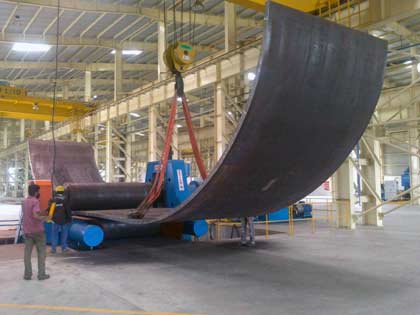
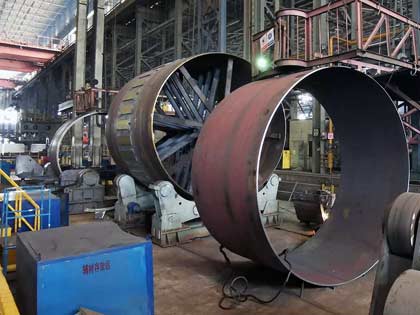
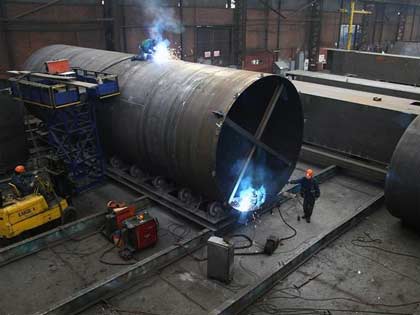
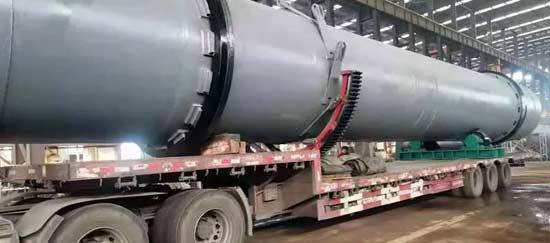
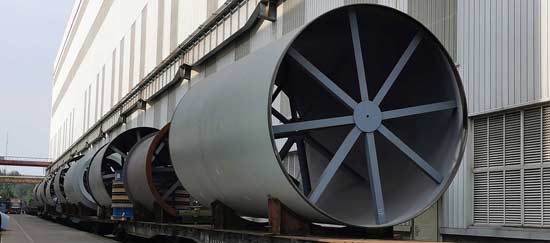
The rotary kiln shell is generally made of steel plates of different thicknesses, which are first rolled into sections of rotary kiln cylinders, and then each section is connected to a long cylinder. Steel plate thickness depends on the specifications of rotary kiln and raw material, which needs to be determined by calculation. Usually, several specifications such as 18, 20, 25, 28, and 32 mm are used. In order to enhance rotary kiln shell rigidity and reduce radial deformation at the support belt, thicker steel plates are adopted at the first section of rotary kiln head, which are subjected to greater stress, are even 40, 50, 60, 665, 75 mm thick. In addition thick steel plate are also used for the cylinder at the support wheel belt, a backing plate with several soil blocks evenly distributed is also installed on the circumference. This can make the rotating damage cylinder more uniform, prevent the rotary kiln shell from being worn by the wheel belt, and also provide better heat dissipation conditions.
Maintenance of Rotary Kiln Shell
After a long-term operation, large rotary kiln and grinding mill always begin to have various problems. Once a rotary kiln accident occurs, it will cause huge loss because of production stoppage. Therefore, regular maintenance of large rotary kiln and grinding mill, and spare parts replacement can effectively extend the service life of rotary kiln.
Rotary Kiln is always a key production equipment in various industries, good maintenance work of large equipment such as rotary kiln, ball mill, grinding mill will avoid accident due to equipment failures in your production, spare parts of rotary kiln shall be replaced timely when it is in bad condition. Rotary Kiln Shell is the main body of rotary kiln, if it is found to have been deformed, customer shall check out if it need to be replaced before it lead to a production accident.
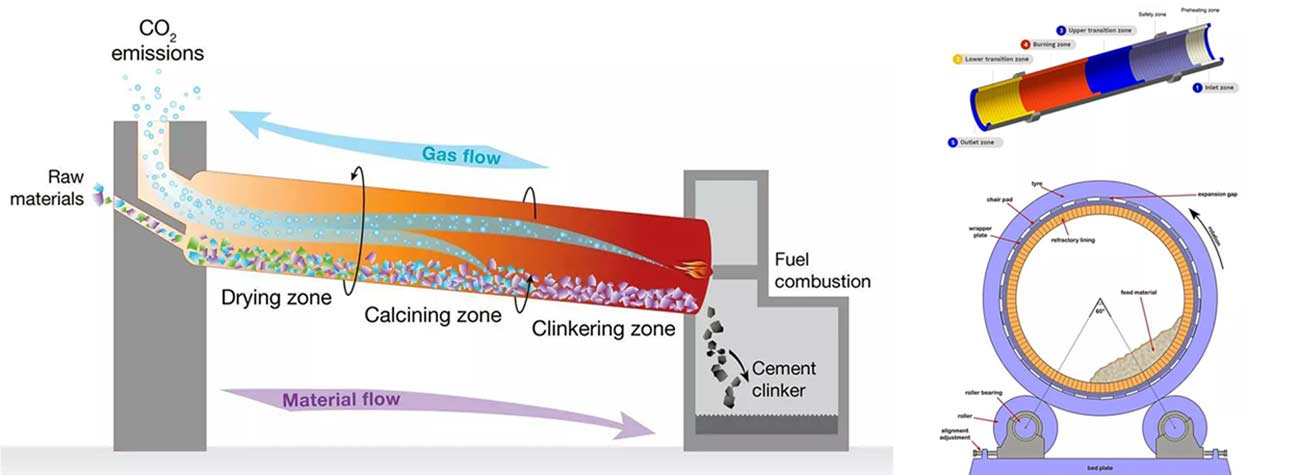
As an top mining machinery supplier for large ball mill and rotary kilns, AGICO is able to produce large forging spare part 1-150tons/pc for cement, metallurgy, mining and other industries, such as girth gear for rotary kiln and ball mill, vertical mill roller, rotary kiln shell, etc. AGICO is one of the largest suppliers for many mining and cement production factories in China and abroad.
Manufacturing process: blanking, coiling, welding, heat treatment, shot blasting, rust removal, painting, packaging.
Agico designs specific manufacturing and welding processes of single-segment shells according to drawing details. After the assembly and welding, then post-weld treatment is performed, including non-destructive testing, post-weld heat treatment, and pressure resistance test to ensure the high quality of kiln shell.
Kiln Shell Customized for Various Rotary Kilns
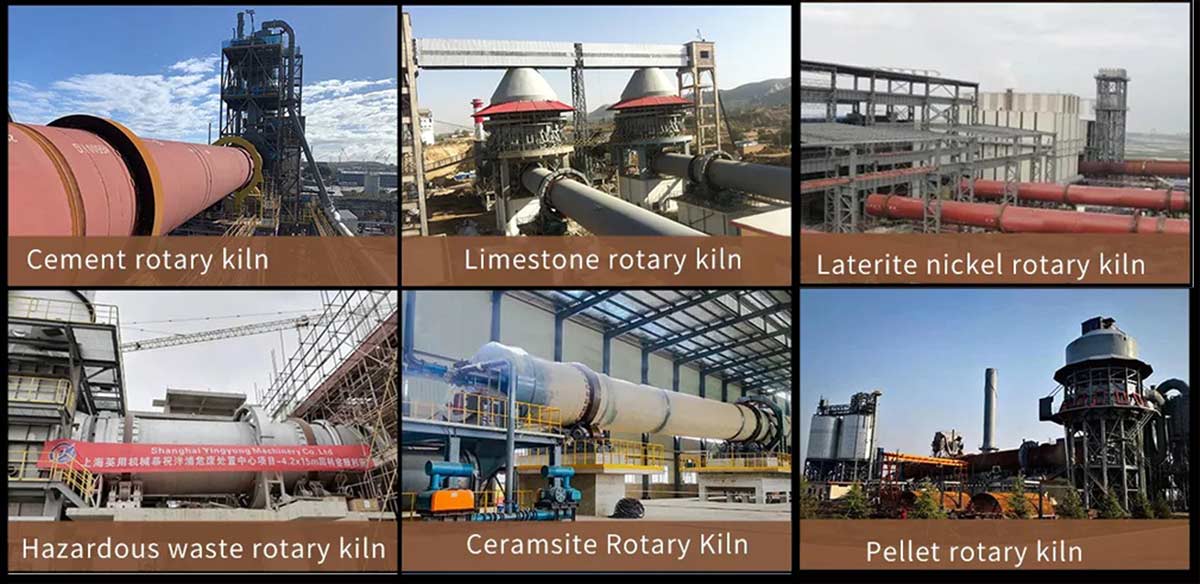
Rotary Kiln Specifications and Size
Rotary kiln Specifications | Rotary kiln Size |
Yield (t/d) |
Rotating speed (r/min) |
Motor Power (Kw) |
Gross weight (t) |
||
---|---|---|---|---|---|---|---|
Diameter/m | Length/m | Slope/% | |||||
Φ2.5×40 | 2.5 | 40 | 3.5 | 180 | 0.44-2.44 | 55 | 149.6 |
Φ2.5×50 | 2.5 | 50 | 3 | 200 | 0.62-1.86 | 55 | 183.7 |
Φ2.5×54 | 2.5 | 54 | 3.5 | 204 | 0.48-1.45 | 55 | 196.2 |
Φ2.7×42 | 2.7 | 42 | 3.5 | 320 | 0.10-1.52 | 55 | 198.5 |
Φ2.8×44 | 2.8 | 44 | 3.5 | 400 | 0.44-2.18 | 55 | 201.6 |
Φ3.0×45 | 3.0 | 45 | 3.5 | 500 | 0.5-2.47 | 75 | 210.9 |
Φ3.0×48 | 3.0 | 48 | 3.5 | 700 | 0.6-3.48 | 100 | 237 |
Φ3.0×60 | 3.0 | 60 | 3.5 | 300 | 0.3-2.0 | 100 | 310 |
Φ3.2×50 | 3.2 | 50 | 4.0 | 1000 | 0.60-3.0 | 125 | 278 |
Φ3.3×52 | 3.3 | 52 | 3.5 | 1300 | 0.27-2.66 | 125 | 283 |
Φ3.5×54 | 3.5 | 54 | 3.5 | 1500 | 0.55-3.40 | 220 | 363 |
Φ4.0×56 | 4.0 | 56 | 4.0 | 2300 | 0.41-4.07 | 315 | 456 |
Φ4.0×60 | 4.0 | 60 | 3.5 | 2500 | 0.40-3.96 | 315 | 510 |
Φ4.2×60 | 4.2 | 60 | 4.0 | 2750 | 0.4-3.98 | 375 | 633 |
Φ4.3×60 | 4.3 | 60 | 3.5 | 3200 | 0.40-3.96 | 375 | 583 |
Φ4.5×66 | 4.5 | 66 | 3.5 | 4000 | 0.41-4.1 | 560 | 710.4 |
Φ4.7×74 | 4.7 | 74 | 4.0 | 4500 | 0.35-4.0 | 630 | 849 |
Φ4.8×74 | 4.8 | 74 | 4.0 | 5000 | 0.40-3.96 | 630 | 899 |
Φ5.0×74 | 5.0 | 74 | 4.0 | 6000 | 0.35-4.0 | 710 | 944 |
Φ5.6×87 | 5.6 | 87 | 4.0 | 8000 | Max4.23 | 800 | 1265 |
Φ6.0×95 | 6.0 | 95 | 4.0 | 10000 | Max5 | 950×2 | 1659 |
Spare Parts AGICO Supplies
As a well-known service provider for large kiln and grinding mill, AGICO can produce large mechanical spare parts (1-150tons/piece) for building materials, cement, metallurgy, mining and other industrial industries, including ball mill trunnion, girth gear, vertical mill roller and table, rotary kiln shell, support roller, etc. AGICO is the large parts supplier for many famous enterprises such as China National Building Material Group, Shanshui Cement, Lafarge, Taimu, and Wannianqing cement, TaTa.