Disc Granulator
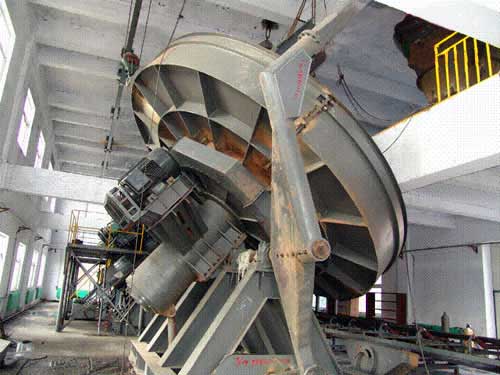
Disc Granulator Introduction
Ball forming disc is also called disc granulator, which can be used for various dry powder granulation and dry powder pre-wet granulation. The effect of pre-wet granulation is good, so it should be preferred. It is the main equipment for forming powdery materials into balls. It has the advantages of uniform ball forming, easy control of ball moisture, high ball strength, simple structure, convenient control, low power consumption, and stable operation. Mainly used in cement, chemical industry, metallurgy, mining and other industries.
Disc Granulator Working principle:
The raw meal powder is evenly moistened by atomized water in the twin-shaft mixer to form a ball nucleus with a very uniform particle size, and then sent to the ball forming plate for ball formation. The water content of the material ball should be controlled at 12--14%. Most of the water should be added in the twin-shaft mixer, and only a small amount of water should be added to the ball forming plate, and the amount of additional water should be controlled at about 0--3%. Dry powder granulation is directly added to the ball forming tray and sprayed with an appropriate amount of water. After the raw material ball core enters the ball forming disk, it is affected by centrifugal force, friction force and gravity in the disk, and moves along a parabola. Due to the cohesiveness and plasticity of the material, the ball cores are bonded to each other and gradually grow up during the movement. When the inclination angle of the ball plate, the height of the edge of the plate, the rotation speed and the water content are considered, the material balls with different particle diameters will leave the edge of the plate and roll down at different angles of separation due to the difference in gravity. In the process of continuous rolling, the water in the ball is continuously discharged out of the surface. Due to the cohesiveness of the material and the natural volatilization of the liquid film on the surface, the ball has strength. The edges are drained out of the tray. The pellets produced by the equipment are beneficial to the improvement of clinker output and quality.
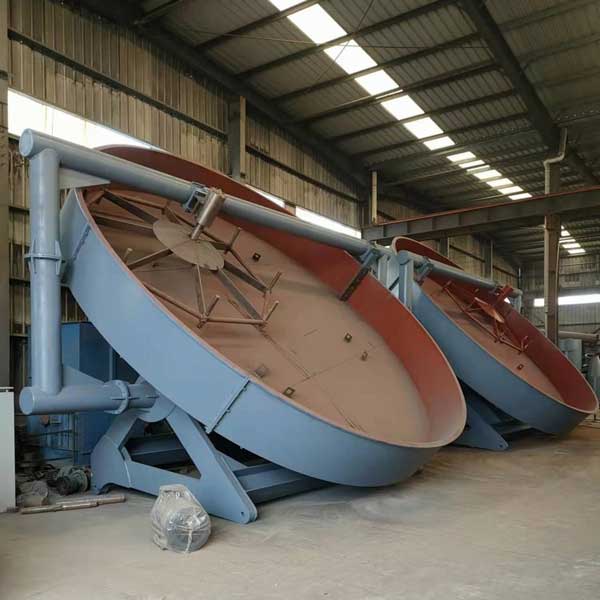
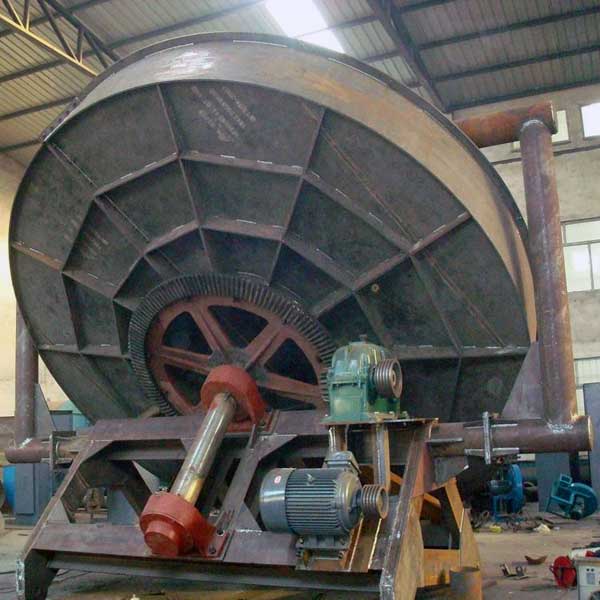
The disc pelletizer is the equipment for manufacturing green pellets in the pellet production process. When the disc rotates around the central axis (or center line), the ball-forming material rolls down along the bottom of the disc, and the fine-grained material is scattered on the surface of the wet cue ball, so that the cue ball continues to grow to the specified size. Its working characteristics: It can make the material form a regular movement, so that the larger pellets and the smaller pellets run along their own different orbits, so they can be classified according to the size, and the green pellets with a qualified size are discharged.
Why Choose Disc Pelletizer Machine From AGICO
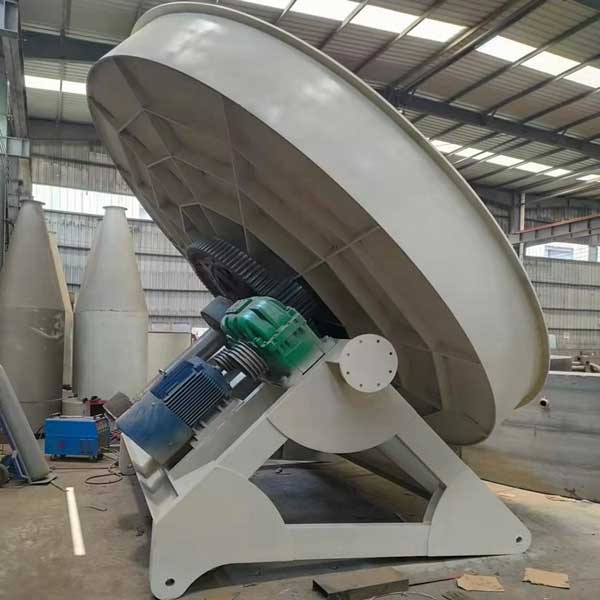
The disc pelletizer machine designed and manufactured by our company is designed and developed after absorbing advanced experience at home and abroad. The product adopts an electric rotary scraper to scrape the surface of the disc to granulate and pelletize, which has strong adaptability; the inclination and speed can be adjusted; the structure is a simple counterflow type, which is easy to install and maintain; it has strong production capacity, high efficiency and large output. The main technical indicators have reached the leading position in the country. According to the needs of users, we can design and manufacture disc pelletizers of different specifications and models. Our products have high pelleting rate and strong raw material adaptability. Both magnetite and hematite fine powder can be used, and the pellets produced have high iron content, good metallurgical performance, and are suitable for long-term storage and long-distance transportation. Commoditization advantage.
Disc Pelletizer Machine Types
According to different equipment structures, it can be divided into two types: slewing bearing type disc pelletizing machine and large and small gear type disc pelletizing machine. The commonly used specification model in the market is φ6000 disc pelletizing machine, small equipment is divided into φ3500, φ4500, φ5500, etc., and large equipment is divided into φ7000 and φ7500. Production lines with different outputs are adjusted by increasing or decreasing the number of pelletizing discs.