Belt Sintering Machine

What is Belt Sintering Machine
The sintering machine is not a machine, but a project consisting of several processes. Take the 48-square-meter laterite nickel ore sintering machine project as an example:
the main sections of the sintering machine consists of the following: quicklime crushing Room, coal (coke) powder crushing room, raw material warehouse, primary mixing room, secondary mixing room, 70m2 sintering room, binder, thermal breaker, screening room, etc.
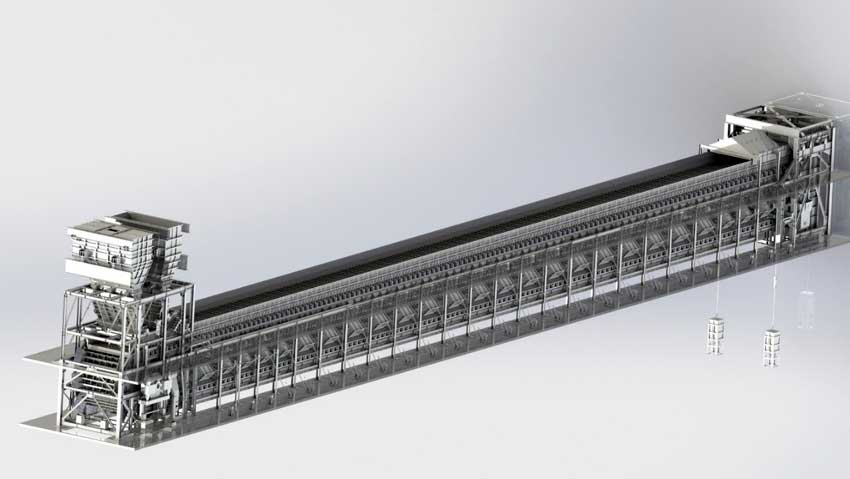
Raw material warehouse
The raw material warehouse (60×80m) is equipped with 2 50-type loaders and one 5*8-meter slide screen, which is used for drying and screening raw ore mixed lime, and is used as a reserve warehouse for sinter production. There are 6 silos, the mineral powder and fuel are weighed by electronic scales, and the flux is dosed by screw feeding scales according to the set ratio, and then sent to the mixing machine room by the main batching belt.
Mixing room
The mixing room is equipped with 2 sets of φ2.2×9m mixing machines, and the raw material is mixed with water to a certain humidity and fully mixed. In the secondary mixing, the mixture is pelletized and heated to sinter the mixture.
In the sintering chamber, the mixture is evenly distributed in the mixing bin along the length direction by the shuttle distributor, and then the mixture is evenly and evenly distributed on the 1.5-meter-wide sintering pan by the combination of the round roller distributor and the multi-roll distributor. As the large plate rotates forward, it is sent into the igniter. The mixture preheated by the hot air is heated and ignited by the high-temperature flue gas of combustion. Under the action of negative pressure draft, it burns downward while moving forward with the trolley, and the physical and chemical changes are completed at the tail of the machine. The hot sinter is covered by φ1.5 ×2.0m single-roll crushing and falling into the screening system.
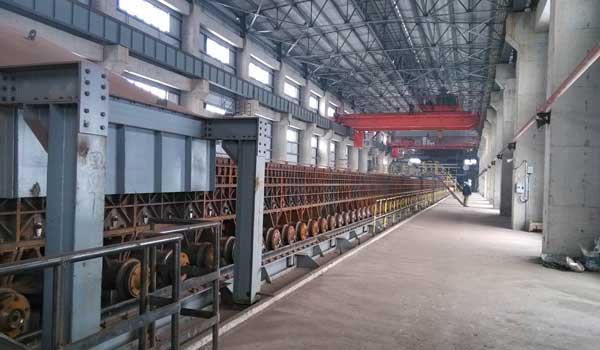
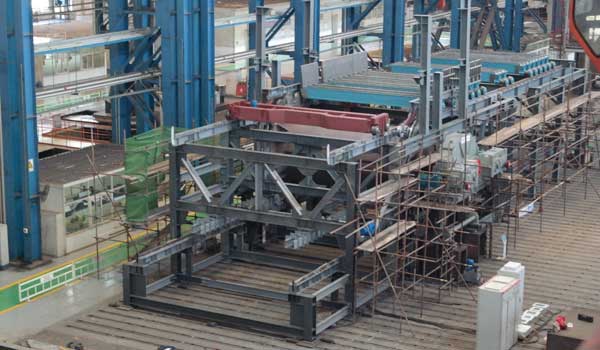
Quicklime crushing chamber
The large pieces of quicklime that have passed the inspection are crushed and screened by jaws and rollers to <3mm>85% of the lime powder is sent to the flux chamber, and then weighed and digested to participate in the batching.
Coal (coke) powder crushing chamber
The coal (coke) powder that has passed the inspection is crushed and screened by four rollers to <3mm> 85% of the fuel powder is sent to the fuel bin, and it is weighed and fed to participate in the batching.
Sinter plant
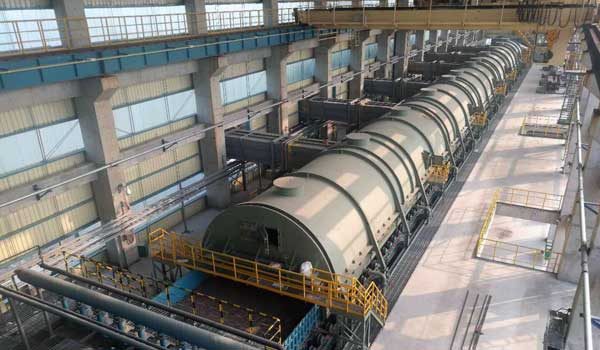
The belt-type sintering machine is driven by the head and tail wheels to move the trolley equipped with the sintering mixture. The bottom material and raw materials are added to the head and ignited. Within the effective sintering length, the mixture is burned from top to bottom to form a hot sinter . In the sintering process, it also has the function of eliminating harmful substances such as phosphorus, sulfur, and arsenic. The belt sintering machine produces sinter, which has the characteristics of large output, good quality, high firing rate, energy saving, convenient use and maintenance, long service life, etc., and plays an important role in the environmental protection of metallurgical enterprises.
The progressive sintering machine is pushed out by the hydraulic system of the head to the trolley equipped with sintering mixture, and the trolley makes reciprocating motion on the return track on the other side of the track. The gas is ignited at the head, and the mixture is burned from top to bottom to form sintered ore, which is cooled on the main machine, crushed by a single roll crusher, and then used for ironmaking in the blast furnace.
Belt sintering Machine working process
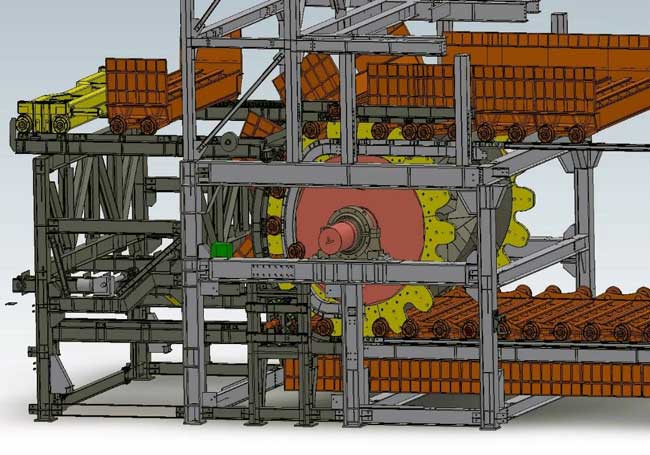
It means that under the action of fuel combustion in the mixture, high temperature and a series of physical and chemical changes, the surface of some mixture particles softens and melts to produce a certain liquid phase and wet other unmelted ore particles. After cooling, the liquid phase binds the ore powder particles into blocks, which is called sintering.
Type |
Effective Sintering area (m 2 ) |
Effective size of Pallet (Width × Length) (m) |
Effective length (m) |
Pallet move speed (m/min) |
Airbox and max load MPa |
Output Under Utilization factor t/h |
||
1.2 | 1.5 | 1.8 | ||||||
KSH-18 | 18 | 1.5×1 | 12 | 0.6-1.8 | ≥ 0.0083 | 21.6 | 27 | 32.1 |
KSH-24 | twenty four | 1.5×1 | 16 | 0.84-2.4 | ≥ 0.0083 | 28.8 | 36 | 43.2 |
KSH-36 | 36 | 1.5×1 | twenty four | 1.2-3.6 | ≥ 0.0088 | 43.2 | 54 | 64.8 |
KSH-50 | 50 | 2×1 | 25 | 1.2-3.6 | ≥ 0.0088 | 60 | 75 | 90 |
KSH-75 | 75 | 2.5×1 | 30 | 1.4-4.2 | ≥ 0.0098 | 90 | 113 | 135 |
KSH-90 | 90 | 2.5×1 | 36 | 1.7-5.1 | ≥ 0.0098 | 108 | 135 | 162 |
KSH-130 | 130 | 2.5×1 | 52 | 2.4-7.2 | ≥ 0.0098 | 156 | 195 | 234 |
KSH-180 | 180 | 3×1 | 60 | 1.59-4.77 | ≥ 0.0137 | 216 | 270 | 324 |
52 | 1.36-4.08 | ≥ 0.0137 | 216 | 270 | 324 | |||
KSH-265 | 265 | 3.5×1.5 | 88.33 | 2.11-6.33 | ≥ 0.0137 | 318 | 397.5 | 477 |
75.75 | 1.81-5.43 | ≥ 0.0137 | 318 | 397.5 | 477 | |||
KSH-300 | 300 | 4×1.5 | 75 | 1.79-5.37 | ≥ 0.0137 | 360 | 450 | 540 |
KSH-450 | 450 | 5×1.5 | 90 | 1.9-5.7 | ≥ 0.0137 | 540 | 675 | 810 |