Pusher Kiln
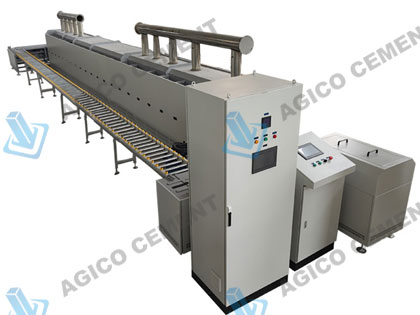
Pusher Kiln For Lithium-Ion Battery
- Usage: Firing of alumina, zirconia, and electronic ceramics
- Maximum temperature: 1650℃
- Furnace cavity size: W850×H390×L20000mm Max.L=40 m
- Working Temperature: up to 1300℃;
- Application: It is mainly used for the mass production of lithium battery cathode materials like lithium iron phosphate, NCA materials, and lithium battery graphite anode materials.
Pusher Kiln Model Specification:
Pusher Kiln Model | RA13-72×2200×25/UM | RA13-84×3600×35/UM |
---|---|---|
Furnace length (m) | 22 | 36 |
Furnace mouth size (mm) | 720×250 | 840×350 |
Maximum operating temperature (°C) | 1300 | 1300 |
Temperature uniformity in high temperature zone (℃) | ±3 | ±3 |
Surface temperature rise (℃) | ≤45 | ≤45 |
Oxygen content | ≤100ppm | ≤100ppm |
Communication Interface | RS-485, RS-232, Modbus RTU | RS-485, RS-232, Modbus RTU |
Pusher Kiln Structure
The pusher type furnace is designed for continous sintering production, which consists of a fully sealed furnace body, transition cabin, pipelines, hydraulic system, feeding control system, temperature control system, etc.

What is a pusher kiln
A pusher type kiln or pusher furnace is a continuous industrial furnace used for high-temperature processes, where materials are pushed through the heating chamber on a fixed path. As the heating chamber can be designed with large length range, it can be used for large-scale production and is capable of maintaining precise temperature control.
Pusher Kiln Design: Pusher kiln is manufactured with sections for preheating, firing, and cooling, and can operate under various atmospheres (e.g., inert gases) to prevent oxidation or other reactions. Pusher kilns are widely used in ceramics, metallurgy, and material synthesis for processes such as sintering for acthode and anode materials, annealing, and calcination.
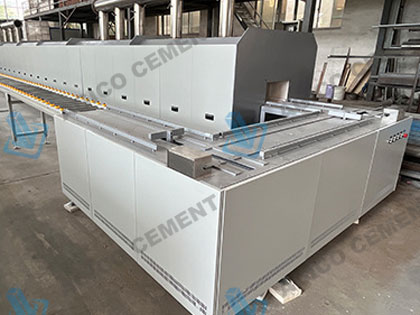
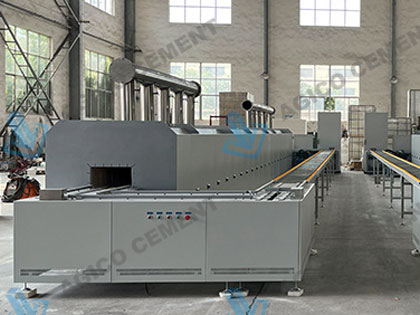
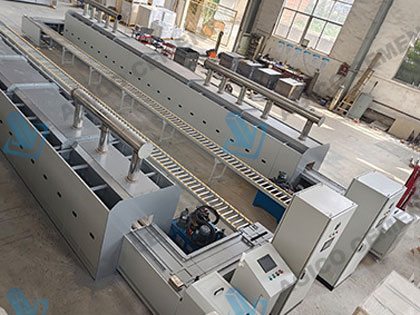
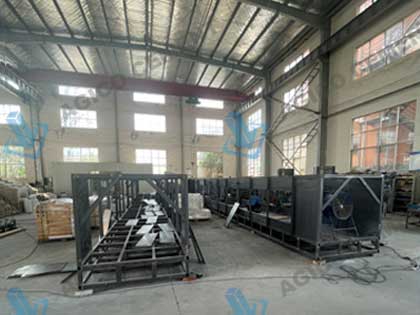
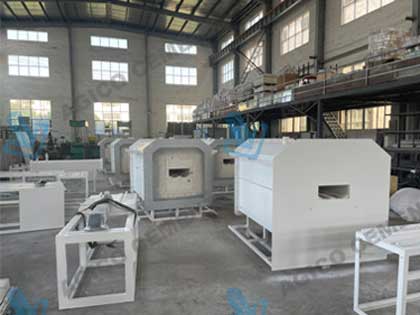
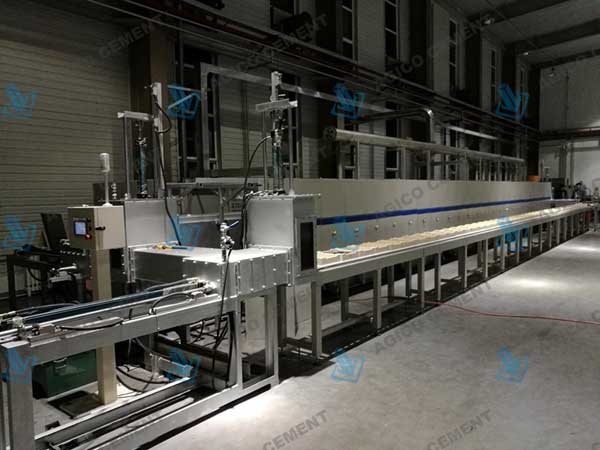
Same as other kiln types, Pusher Type Kiln is also customized into 2 types: Atmosphere Furnace and Air Furnace, here are their applications in the sintering for lithium-lon barttery powder materials:
Atmosphere Furnace For Cathode Materials Sintering
Materials like lithium iron phosphate (LiFePO4) and NCA (Nickel Cobalt Aluminum) require controlled atmospheres (often inert or reducing) to prevent oxidation and ensure proper material properties.
Air Furnace For Anode Materials Sintering
Graphite anode materials do not require the same level of atmospheric control and can be processed in normal air environments.
Pusher Kiln Design Features
- Efficient Operation: Quick atmosphere adjustments and precise control systems.
- Energy Saving: Optimized roof design for energy efficiency and uniform heating.
- Airtight Performance: Fully sealed heating boxes ensure airtightness.
- Accurate Temperature Control: AI-driven temperature regulation for precise control.
- Automated Handling: Automatic material transport, counting, and cleaning.
Why Choose AGICO
- High-Temperature Operation: The push plate furnace can reach up to 1600°C, suitable for the high-temperature treatment needs of hard carbon anode materials.
- High Capacity: With an annual production capacity of 100 tons, it meets large-scale industrial production requirements, enhancing production efficiency.
- Inert Atmosphere Protection: Utilizes nitrogen and other inert atmospheres to prevent oxidation, ensuring stable processing of hard carbon anode materials at high temperatures.
- Eco-Friendly Design: Equipped with an efficient exhaust system to control emissions and reduce environmental impact.
- Flexible Operation Control: Features an advanced automation system for precise temperature control and operation monitoring, ensuring product consistency and quality.