Set Up an Eco-Friendly Design Concrete Batching Plant from AGICO
Concrete Batching Plant With Eco-friendly Design
An Eco-friendly concrete batching plant is an innovative piece of equipment that provides excellent sealing performance. It is designed for efficiency and energy savings, while also prioritizing environmental protection. Key features include noise reduction, dust removal, and wastewater treatment. This type of batching plant is ideal for large-scale concrete production, making it suitable for commercial concrete production companies, water conservancy projects, construction projects, and commercial concrete batching plants.
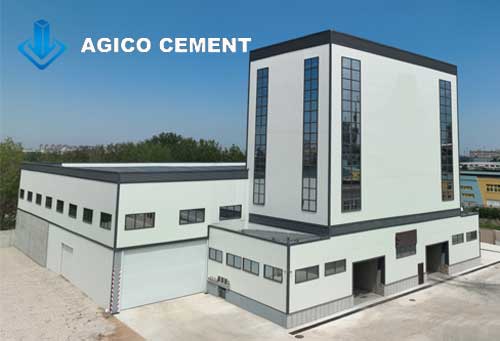
Eco-Friendly Concrete Batching Plant
AGICO offers concrete batching plants with eco-friendly designs with the following specifications, which can be customized for customers’ requirements.- Theoretical production capacity: 25-240 m3/h
- Mixer model: JS500, JS750, JS1000, JS1500, JS2000, JS3000, JS4000
- Dimensions: related to its capacity and other parameters
- Standard discharge height: 1.5-4m
Upgrade Concrete Batching Plants With Eco-Friendly Design
AGICO supplies an Eco-friendly concrete batching plant that utilizes independent research and development technologies, adhering to strict domestic environmental protection standards. The entire batching plant has the advantages of high mixing quality, strong mixing, ecological protection.
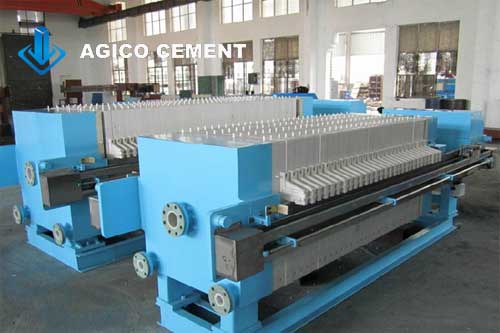
Filter Press
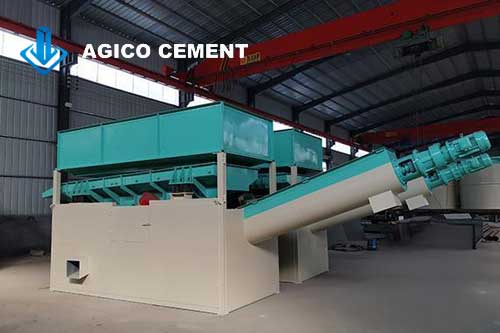
Sand and Gravel Separator
Eco Powder Material Delivery
All powder materials in the Eco-friendly concrete batching plant are transported, measured, and delivered in a closed state, which eliminates dust emissions.
Eco Mixing and Packaging
All components utilize transmission mechanisms that ensure reliable performance and smooth operation, significantly reducing noise levels. The main mixing station and belt conveyor are both equipped with Eco-friendly outer packaging, further minimizing dust and noise pollution.
Upgrade To Eco-Friendly Design
In recent years, the government has become more concerned about environmental protection. This focus necessitates additional environmental factors when planning and constructing concrete batching plants. As a result, many manufacturers have started to prioritize production and upgrade concrete batching plants with Eco-friendly designs.
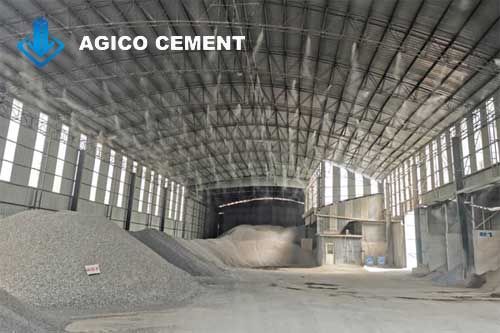
Dust Spraying System
- Closed material yard: The concrete batching plant can be housed in a closed space for the stacking and transporting of aggregates ( sand and stone), this setup ensures that dust and noise emissions from the material yard comply with prescribed standards.
- Overall packaging of the main building: The main building is designed to be dust-proof and noise-reducing, featuring a beautiful and elegant appearance with customized functions.
- Automatic Aggregate Feeding System: This system is designed to feed sand and gravel into the mixing equipment during nighttime operations. It eliminates the need for a loader, allowing for an unattended batching plant that operates normally at night.
- Complete Dust Collection Design: The dust collection system consists of both forced dust collection and bag dust collection methods. These systems effectively manage dust emissions from various points within the batching plant.
- 0 Waste Discharge: collection and reuse of wastewater at environmentally friendly concrete batching plants, along with recycling of waste materials and slurry.
Learn About Eco-Friendly Concrete Batching Plants
Eco-friendly Mixing Solutions The Eco-friendly concrete mixing plant (station) utilizes a high-quality, energy-saving, waste-recycling concept, ensuring the production of green, high-performance concrete. Its closed system for weighing and transporting sand and gravel effectively eliminates issues with dust and environmental pollution during concrete production. This system not only conserves energy but also protects the environment. Additionally, it features equipment for the separation and recycling of wet concrete.
- Sustainable Production Design: The Eco-friendly concrete batching plant combines an attractive design with low carbon emissions and energy efficiency, ensuring high production effectiveness. It recycles wastewater and waste residue, and waste concrete can be transformed into small components for reuse. The production equipment operates without running, bubbling, dripping, or leaking, which helps maintain the stability of concrete production quality.
- Efficient Material Delivery: The powder air trough is designed for conveying dry particles efficiently from top to bottom, achieving effective material transfer. It is energy-saving, noise-free, maintenance-free, and offers precise metering.
- High-Efficiency Dust Management: The pulse bag dust collector boasts a dust removal efficiency of up to 99.9% and requires low maintenance. Its large fan actively draws in air, helping to balance the pressure across various systems in the main building. This ensures accurate metering and an efficient material discharge speed.
- Precise Measurement: Accurate measurements are ensured through automatic deductions for overweight materials and supplementary weighing for underweight ones. The material yard utilizes a belt conveyor for loading, which not only minimizes noise but also effectively controls dust. This approach saves on labor and loader costs while meeting the standards of modern, Eco-friendly batching plants.
One-Stop Service for Eco-Friendly Batching Plant Set Up
After years of research, development, and practical experience, we have sorted and summarized information related to concrete mixing stations. As a manufacturer and supplier of concrete mixing equipment for large, medium, and small stations, we offer customized production line solutions at no cost. We also provide supporting mixing equipment. Our solutions not only enhance the overall output of the mixing station production line but also reduce investment costs for our customers, ensuring we meet the diverse needs of different client groups.
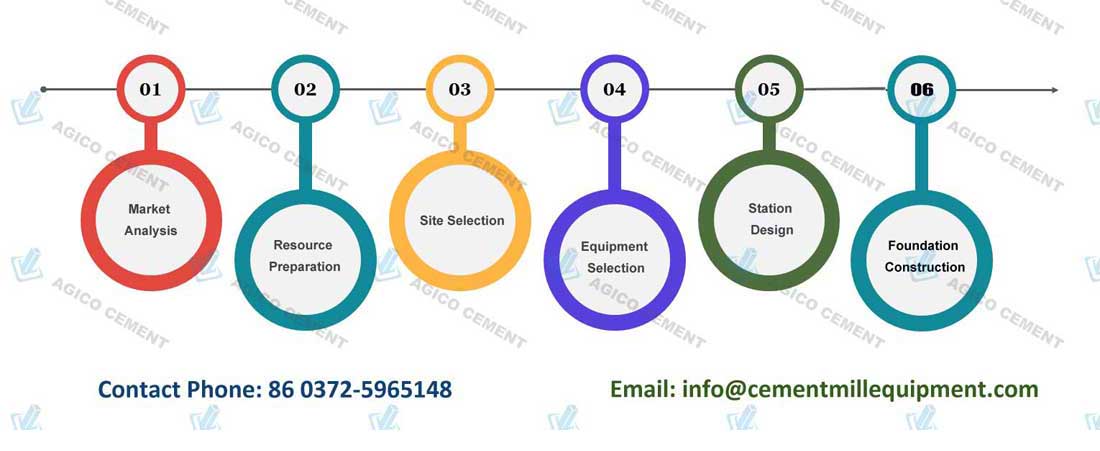
Why Choose Concrete Batching Plant from AGICO
Advanced Concrete Batching Plant Projects
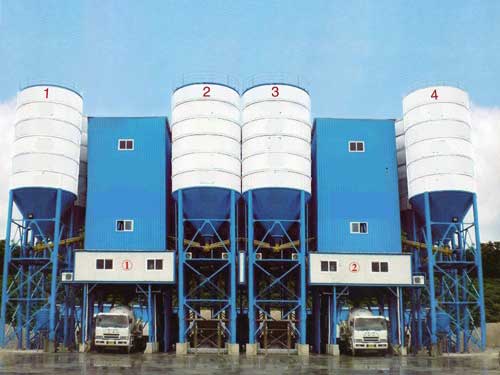
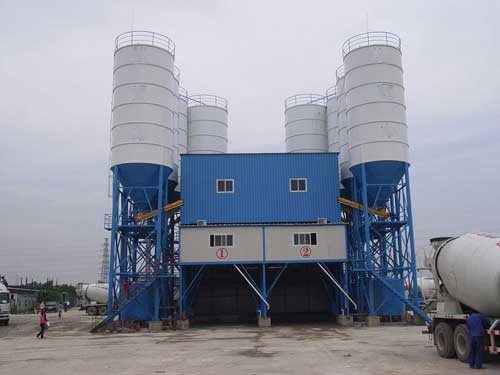
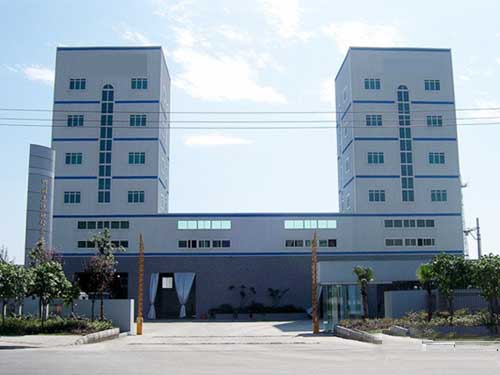
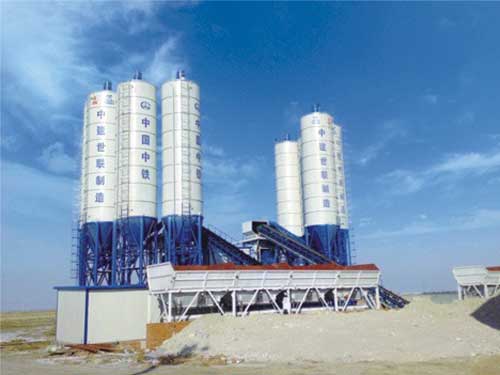
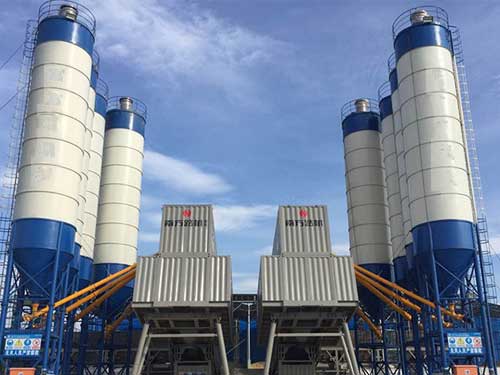
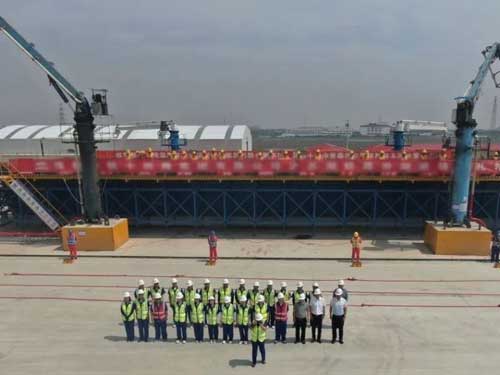
Concrete Batching Plant | Model | HZS 25 | HZS 35 | HZS 50 | HZS 60 | HZS 75 | HZS 90 | HZS 120 | HZS 180 | HZS 240 |
Theoretical Productivity (m3/h) | 25 | 35 | 50 | 60 | 75 | 90 | 120 | 180 | 240 | |
Standard Discharge Height (m) | 1.5 -3.8 | 1.6 38 | 2.7 -3.8 | 3.8 | 2.7 -3.8 | 3.8 | 4 | 4 | 4.2 | |
Working Cycle Time(s) | 72 | 72 | 72 | 60 | 72 | 60 | 60 | 60 | 60 | |
Overall Dimensions (mm) (length*width*height) | 11693* 13060* 17245 | 12922* 13000*17245 | 14950* 17840* 17245 | 36500* 11130* 20400 | 15950* 18840* 17245 | 51093* 19100* 21600 | 55885* 20200* 21600 | 59811*20660*23700 | 56000*22000*21000 | |
Total Capacity(kw) | 50.25 | 75 | 115 | 105 | 120 | 145 | 210 | 260 | 330 | |
Concrete Mixer | Model | JS500 | JS750 | JS1000 | JS1000 | JS1500 | JS1500 | JS2000 | JS3000 | JS4000 |
Batching Machine | Model | PLD 1200 | PLD 1200 | PLD 1600 | PLD 1600 | PLD 2400 | PLD 2400 | PLD 3200 | PLD 4800 | Ground floor type |
Silo Capacity (m3) | 3.5 | 3.5 | 5 | 12 | 15 | 15 | 18 | 25 | 35-50 | |
Pneumatic System | Air Compressor Model | 1.0-7 | 1.0-7 | 1.0-7 | 1.5-7 | 1.0-7 | 1.8-7 | 1.8-7 | 1.8-7 | 1.8-7 |
Rated Exhaust Volume (m3/min) | 1.67 | 1.67 | 1.67 | 1.67 | 1.85 | 1.67 | 1.67 | 1.67 | 1.67 | |
Rated Exhaust Pressure (MPa) | 0.8 | 0.8 | 0.8 | 0.8 | 0.8 | 0.8 | 0.8 | 0.8 | 0.8 | |
Motor Power (KW) | 2.2 | 2.2 | 5.5 | 7.5 | 11 | 11 | 15 | 18.5 | 18.5 | |
Weighing System | Sand and gravel measurement accuracy range (kg) accuracy | ±2% | ±2% | ±2% | ±2% | ±2% | ±2% | ±2% | ±2% | ±2% |
Cement metering accuracy range (kg) accuracy | ±1% | ±1% | ±1% | ±1% | ±1% | ±1% | ±1% | ±1% | ±1% | |
Water metering accuracy range (kg) accuracy | ±1% | ±1% | ±1% | ±1% | ±1% | ±1% | ±1% | ±1% | ±1% | |
Additive metering accuracy range (kg) Accuracy | ±1% | ±1% | ±1% | ±1% | ±1% | ±1% | ±1% | ±1% | ±1% | |
Screw Conveyor | Matching stacking model (m) | LSY219 -6 | LSY219 -6 | LSY219 -9 | LSY219 -9 | LSY219 -9 | LSY219 -9 | LSY219 -9 | LSY325 | LSY325 |
Motor power (kw) | 7.5 | 7.5 | 11 | 11 | 11 | 11 | 15 | 18.5 | 18.5 | |
Number of units | 2 | 2 | 3 | 3 | 4 | 4 | 4 | 4 | 4 |
- High-efficiency batching and mixing equipment
- High-quality batching machine (all imported components, high weighing accuracy and stability)
- High-stability inclined belt conveyor (externally closed structure)
- High-precision weighing system (microcomputer control, high precision, tight sealing)
- High-performance fully automatic microcomputer control system (simulating on-site workflow, full-time monitoring)
- High-standard environmental protection performance (low noise, good dust prevention effect)
- Modular design, humanized service (free design, installation and commissioning guidance, and technician training throughout the process)