Stirred Ball Mill
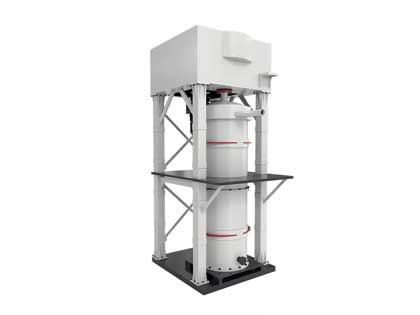
Stirred Ball Mill Introduction
The stirred ball mill is composed of a frame, a stirred system, a control system, a grinding cylinder and a grinding medium. It rotates at high speed through the agitator to make the grinding medium irregular movement. This chaotic movement produces collisions, squeezes, frictions and shears of the abrasive medium, causing the material to be crushed and finely ground.
Stirred ball mill is widely used in zirconium silicate, zirconia, alumina, ceramics, chemicals, electronic materials, magnetic materials, papermaking, coatings, metal or non-metallic minerals, new materials, paints, graphite, calcium carbonate, pharmaceutical and other ultra-fine powder grinding preparation.
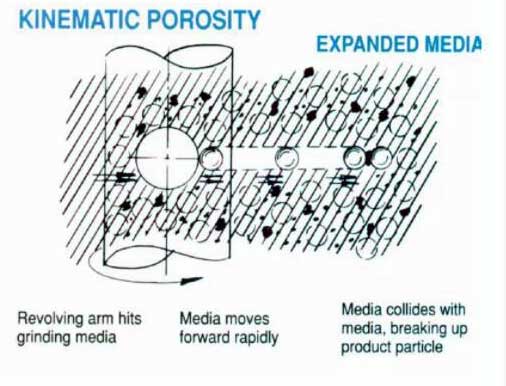
According to the size of the processing amount or the experimental production use, the stirred ball mill can be divided into three categories: small stirred ball mill, light stirred ball mill, and large stirred ball mill. Small stirred ball mill is suitable for scientific research and small tests, light operation and saves materials. Light agitator ball mill is generally suitable for pilot or pilot production, to verify the small test process and can be used for small batch production. Large agitator ball mill for mass production.
A stirred mill is a grinder that contains an internal stirred medium. It is often referred to as a "stirred ball mill"; We can divide it into dry stirred mill, wet stirred mill, normal speed stirred mill and high-speed stirred mill.
A useful and simple equation for describing the amount of grinding momentum is m×v (mass× velocity), which allows us to understand why agitation mills are suitable for grinding. For example, ball mills use large media, usually 12 mm or larger, and operate at low speeds (10-50 rpm). Other agitation mills, such as sand mills, use smaller media of 0.3 mm to 2 mm, but the speed is very high (about 800-1200 rpm), and the speed of the medium-free high-speed disperser is even faster (1200-1800 rpm). The various types of powder mills fall somewhere in between (see the figure below for a comparison of grinders).
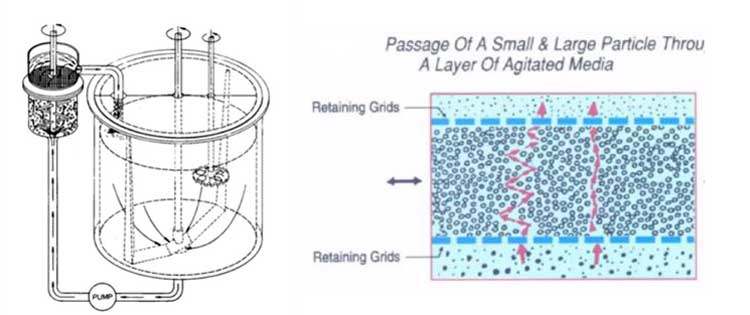
Comparison of agitator ball mills
Type of agitation mill | Grinding size | rotate speed |
End speed (m/S) |
ball mill | 12mm and above | 10-50 | --- |
Agitation mill | 3-10mm | 75-450 | 3-5 |
Sand mill | 0.2 to 2mm | 800-1200 | 10-15 |
HSA agitation mill | 1mm-3mm | 400-1800 | 10-13 |
Q stirred mill | 0.4mm-3mm | 1000-1900 | 15 |
High-speed disperser | --- | 1200-1800 | 25-30 |
Working principle of stirred mill:
The most important concept in the agitation mill is that the power input acts directly on the agitated medium to achieve grinding, rather than acting on the grinding cylinder.
For efficient grinding, both impact and shear forces must be present, as shown in Figure 1. When wet grinding is carried out in the agitation mill, due to the irregular movement of the grinding medium, the continuous impact of the grinding medium will produce an impact effect, and the shear force acts on the stirred mill, because the randomly moving ball (medium) rotates in different directions of rotation, thus applying shear force to the adjacent slurry. Therefore, both liquid shear force and medium impact force are present. This combination of shear and impact effects results in a reduction in the size of the ground material and good dispersion.
The principle of stirred grinding dry grinding is achieved through the motor expansion of the medium, which is called kinematic porosity. Dried particles are subjected to various forces, such as impact, rotation, tumbling and shearing; As a result, fine powders in the micron range can be easily obtained. In addition, the combination of these forces produces more spherical particles than with other impact grinding equipment.
The versatility of the agitation mill is achieved by operating under a wide range of conditions. For example, the type, size and quantity of the grinding medium; Different device speeds; Variable loading capacity or feed rate of raw materials. In addition to reducing the particle size, the agitation mill also enables tight stirred of different materials at the highest strength. Specific chemicals or additives can also be added to the agitation mill during the grinding process for the purpose of final dispersion or coating of dried solid particles.
Agitation mill configuration:
Various types of agitation mills can be used for wet or dry grinding processes.
Specially designed for the ceramic industry to prevent metal particle contamination of the stirred mill. Several types of ceramic and polymer materials have been developed for the manufacture of linings or sleeves for parts inside equipment. Including alumina, zirconia, silicon carbide, silicon nitride, tungsten carbide, rubber, polyurethane and various plastics.
The agitation mill is designed with variable speed drive device, which can be used for different speeds.
Experimental agitation grinding cylinder volumes range from 100ml to 9.5 litres, and production-type agitation mill volumes range from 35 litres to 3800 litres.
All grinding cylinders are equipped with cooling or heating jackets.
Sealed caps are available for grinding in an inert atmosphere.
Agitation and grinding medium selection:
Various types of agitation mills can be used for wet or dry grinding processes.
Specially designed for the ceramic industry to prevent metal particle contamination of the stirred mill. Several types of ceramic and polymer materials have been developed for the manufacture of linings or sleeves for parts inside equipment. Including alumina, zirconia, silicon carbide, silicon nitride, tungsten carbide, rubber, polyurethane and various plastics.
The agitation mill is designed with variable speed drive device, which can be used for different speeds.
Experimental agitation grinding cylinder volumes range from 100ml to 9.5 litres, and production-type agitation mill volumes range from 35 litres to 3800 litres.
All grinding cylinders are equipped with cooling or heating jackets.
Sealed caps are available for grinding in an inert atmosphere.
Media Selection Criteria:
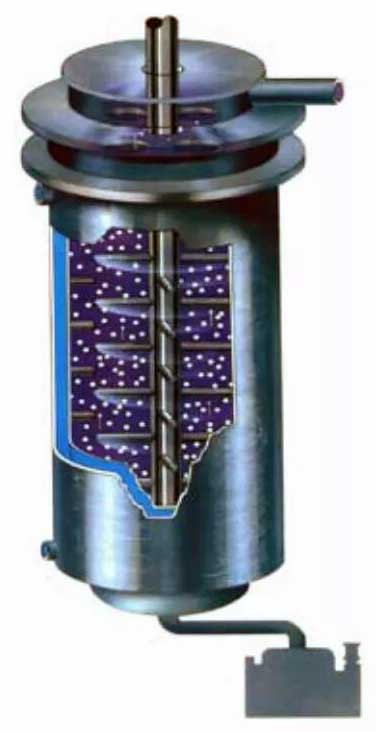
- Density. In general, high-density media work better. The density of the medium should be greater than the density of the material to be ground. When grinding certain slurries, a higher density medium may be required to prevent floating.
- Initial feed size. Smaller media cannot easily break down large particles.
- Final particle size. Smaller media are more efficient when ultrafine particles are required.
- Hardness. The harder the medium, the better the grinding efficiency and the longer the service life.
- PH. Some strongly acidic or alkaline materials may react with certain metal media.
- Color. For example, the white material should remain white with a white grinding ball and lining.
- Pollution. Material worn off by the medium cannot affect the product and can also be removed by magnetic separators, chemicals or sintering processes.
- Cost. Media that are 2-3 times more expensive can be more durable, and sometimes 5-6 times more durable, so their additional cost is worth it in the long run.
The choice of grinding medium depends on several factors, some of which are interrelated.
Stirred Ball Mill Types
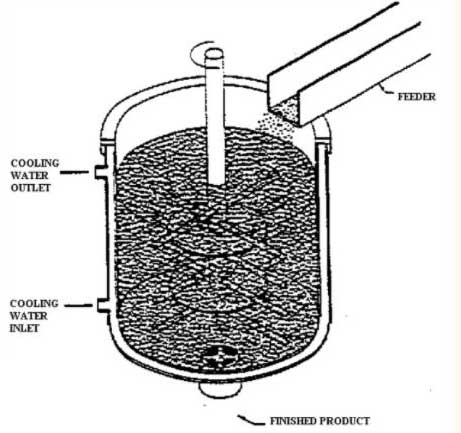
Wet stirred mill type:
>Batch agitation mill ("S" type equipment)
The operation of the batch stirred mill (fig. 2) is very simple. All materials can be loaded directly into the grinding cylinder; No prestirred pre-dispersion is required. Since the top open grinding cylinder is fixed, the process can be observed directly and additional components can be modified and added at any time. If the material is fragile, the maximum feed particle size can reach 10mm; Conversely, any material under 10 mesh can be processed in this machine.
All "S" type equipment is equipped with a pump that maintains circulation during the grinding process to accelerate grinding and uniformity, and the pump can also be used for unloading.
Batch agitation mills are used to process materials that are difficult to grind, such as tungsten carbide, silicon carbide and various metals. High viscosity slurries up to 30,000 cps can also be easily handled in batch agitation mills.
>Circulating agitation mill ("Q" type equipment)
The system consists of a stirred mill and a premix cylinder, and the volume of the premix cylinder is usually 10 times the volume of the agitator grinding cylinder. One of the basic requirements of a Q-type agitation mill system is the high-speed cycle) rate. Convey all the material in the premix cylinder to the agitation mill at least once every 7-8 minutes.
At such a fast speed, the premixed slurry is pumped through the closed media layer. This medium acts as a dynamic sieve, allowing fine particles to pass through quickly, while coarser particles are ground thinner along more tortuous paths. The slurry can be monitored continuously (fig 4), additional components can be added to the premix cylinder at any time during the grinding process, and grinding can be precisely terminated.
Stirred Ball Mill Advantages
One of the advantages of the circulation system is that it is possible to process a large amount of material with less grinding medium and grinding equipment. Another advantage of the "Q" type agitator mill is better temperature control, which is for two reasons:
1. The stirred cylinder has a cooling or heating jacket, which acts as a heat sink.
2. The speed at which the slurry passes through the grinding chamber is very fast (20-30 seconds each), so the heating time is shorter.
These advantages are important when the grinding chamber lining is a material with poor thermal conductivity, such as plastic or rubber
>Continuous agitation mill ("C" or "H" equipment)
Type C equipment is best suited for the continuous production of large quantities of material. The H-type device has the same construction as the C-type device, but uses a smaller medium (2-3mm) and operates 60-70% faster than the C-type device.
Using this type of process requires a sufficiently premixed slurry. The slurry is pumped upward through the high and narrow bottom of the grinding cylinder and discharged from the top of the cylinder. The residence time required for a particular fineness is controlled by the pump speed.
Continuous agitation mills can be set up in series, using larger media and grille openings for coarse feeding, followed by subsequent units using smaller media for finer grinding.