Hydrated Lime Plant

Build Hydrated Lime Plant For Various Industries
AGICO Cement has been supplying various lime processing plants for worldwide customers, inwhich Hydrated lime Production Plant is widely built for Hydrated lime (Ca(OH)2) production in many different industries, such as lime hydration process in sintering dosing chamber of steel plant, quick lime hydration process in desulfurization system, calcium treatment agent preparation process for sewage treatment, fine chemical high-quality hydrated lime (Ca(OH)2) preparation process. The hydration process of quick lime is controlled by multiple processes such as reasonable water distribution in a multistage lime hydrator , and the quick lime is processed into a fluffy hydrated lime dry powder, and the moisture content is controlled to less than 1.5%.
Raw lime (calcium oxide) for Hydrated Lime Production
Activated lime is also known as calcium oxide and comes in different types and qualities, include active lime, ordinary lime and low active lime, here is a brief introduction of all types and specific uses; :
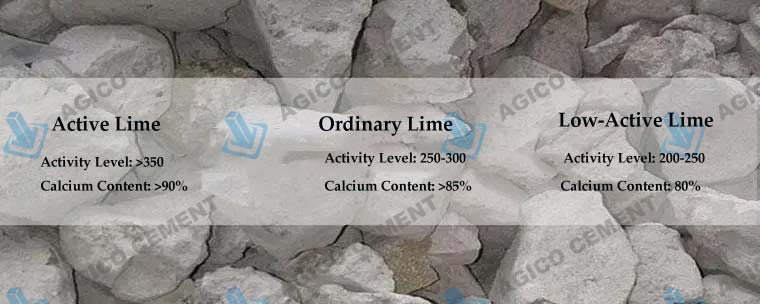
Lime Type | Details |
---|---|
Active Lime |
Activity Level: >350 Manufacture: Produced with rotary kilns and Maerz kilns. Quality: Mainly high-purity, calcium content being usually >90%. Special Products: Useful medicinal and food-grade calcium produced after personal selection and special calcined process with manual selection and keeping high degrees of standard requirements. |
Ordinary Lime |
Activity Level: ~250-300 Manufacture: Shaft kiln lime, rotary kiln, Maerz kiln Quality: Content of effective calcium greater than 85%. |
Low-Active Lime |
Activity Level: About 200-250 Quality: Effective calcium content about 80%. Sources: Commonly has sources including by-products of high-quality hydrated lime production, light calcium, nano calcium manufacture, and calcium carbide slag. |
Uses and Application | Different grades of raw lime materials are utilized to produce different grades of hydrated lime products, which can fulfill various requirements of customers from a variety of end-use industries. The selection of the appropriate grade of raw lime has to meet some specific demands of quality and performance. |
Main Equipment of Hydrated Lime Production Line
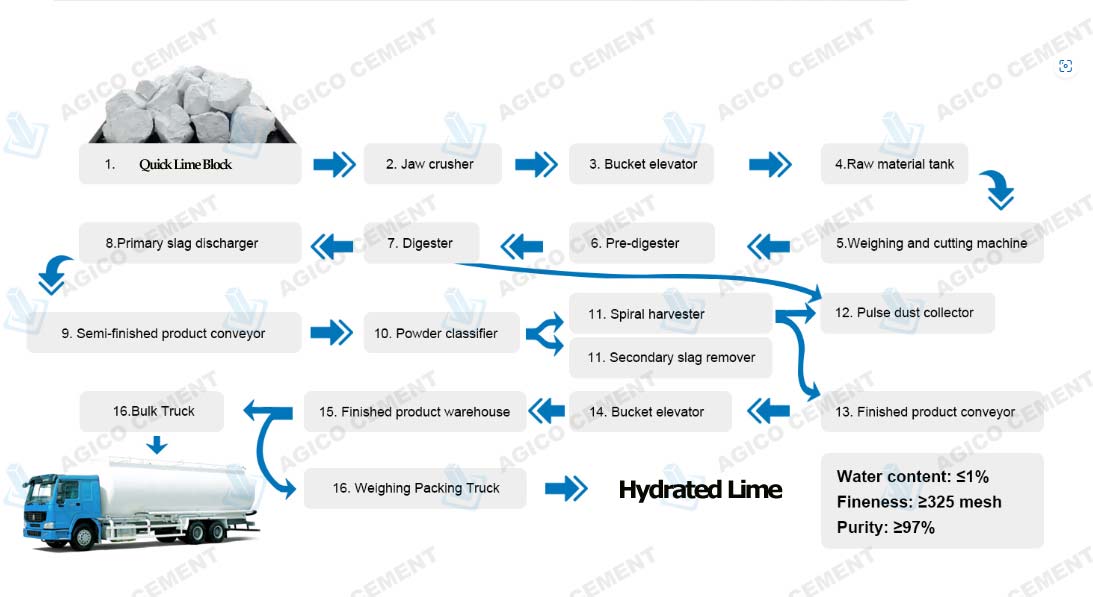
- Crusher: The crusher crushes the limestone into small blocks. Normally, jaw crushers and hammer crushers are used. Choose the appropriate type of crusher based on the hardness and particle size requirements of the raw materials.
- Lime Hydrator: Hydrator is the core device of hydration; it can be classified as a continuous and intermittent hydrator machine. The continuous hydrator is highly automated with a large output, so it is suitable for mass production, while batch hydrators are suitable for small-scale production or experimental research.
- Filter: Used for filtering impurities from lime milk, it is usually a sand filter and cardboard filter. Appropriately choose the type of filter and filter material according to the actual situation.
- Ageing warehouse: The device that ages lime milk, usually in a cylinder or rectangle in shape. Based on the scale of production and process requirements, determine the size and quantity of ageing tanks.
- Dehydrator: Dehydrator is used to remove the water in the lime milk, and the commonly used is vacuum filter and filter press. The vacuum filter is suitable for small-scale production, and the filter press is suitable for large-scale production.
- Screening machine: Screening machine is used to screen the finished Hydrated lime into products with different particle sizes. Commonly used are vibrating screen and drum screen.
Process Flow of Hydrated Lime Production Line
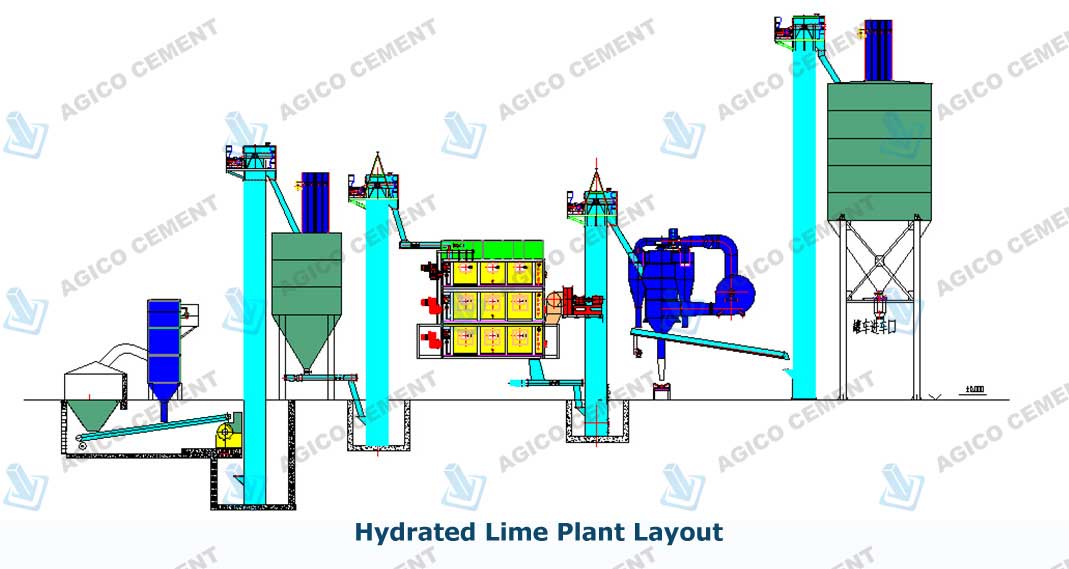
- Raw Material Preparation: Quicklime needs to be crushed and screened to obtain the raw material with uniform particle size. Commonly used raw materials are limestone, dolomite and so on.
- Hydration of Quicklime: the raw materials quick lime after crushing and screening are mixed with appropriate amount of water, and the hydration reaction is carried out in the hydrator machine to generate lime milk. Temperature and PH are controlled to ensure the quality of the milk of lime.
- Lime Milk Purification: There are unhydrated small particles and impurities in lime milk that require purification. Common purification methods include filtration and sedimentation.
- Lime Milk Ageing: Ageing means that in certain temperature and pressure conditions, the lime milk has been fully reacted and is of high quality. The stability of lime milk after ageing is higher and more conducive to the subsequent process.
- Lime Mlk Dehydration: This is the process of removing the water in the lime milk to produce solid Hydrated lime. Common dehydration methods include natural drying and mechanical dehydration.
- Finished Product Packaging: Hydrated lime after dehydration needs to be screened and packaged to meet market demand.
AGICO CEMENT - Advanced Hydrated Lime Production Technology
In turning quicklime into hydrated lime, there will be sophisticated frequency modulation control within the AGICO CEMENT. This precisely controls the amount of water supplemented with the mass, water content, and reaction temperature of quick lime to ensure an appropriate ratio of lime to water for the attainment of an ideal hydration effect.
Why Choose Hydrated Lime Plant from AGICO CEMENT:
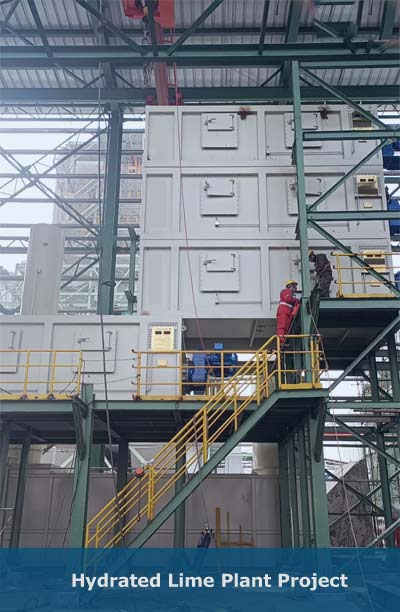
Accurate Water Supply Control:
- The frequency modulation is used to adjust the water flow.
- Ensure proper hydration based on the quicklime quality and its activity.
Optimal Hydration Process:
- Control stirring and advancing speeds that allows adequate time for the ripening and swelling of calcium oxide.
- Enhance completion of the digestion reaction.
Efficient Separator Design:
- The wind wheel and rotor of separator are undergone dynamic and static balance test to ensure that there will be no vibration and low noise.Provides smooth operation and long life for wearing parts.
- Equipped with three mechanical seals at the rotor and body junction, preventing cold particles in the finished product.
High-Quality Finished Product:
- Achieves a finished powder qualification rate of over 98%.
- Features a slag discharge device for complete separation of ash and slag.
- Allows adjustment of finished product fineness up to 600 mesh.
- Uses a closed air discharger to eliminate dust pollution.
Rigorous Quality Control:
- Ensures high-quality equipment through meticulous design, raw material selection, and strict testing.
- Reduces maintenance rates and extends the service life of wearing parts.
- Lowers operational costs and maximizes user benefits.
If you are looking for a Hydrated Lime Plant supplier, feel free to Contact AGICO CEMENT for Tailored Lime Processing Solution now.