Cement Vertical Mill
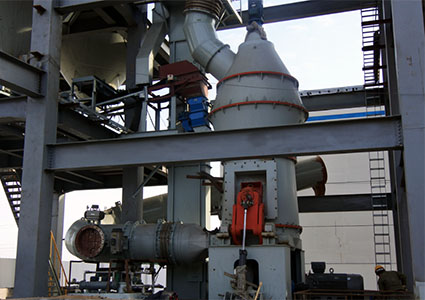
- Applications: Widely used in cement, power, metallurgy, chemical, metal and non-metallic industries due to its high efficiency and energy saving, stable product output.
- Material: can be used for feldspar, calcite, talc, barite, fluorite, rare earth, bentonite, marble, limestone, bauxite, manganese ore, phosphate rock, iron oxide red, quartz sand, cement clinker, activated carbon, clay Processing of non-flammable and explosive mineral powders with a Mohs hardness of 8 or less and a humidity of less than 10%, such as coal gangue, gypsum, silicon carbide, slag, manganese ore, and potassium feldspar.
- Vertical Miller Types: Coal Vertical Mill, Slag Vertical Mill and Cement Vertical Mill
Cement Vertical Mill Description:
The vertical mill is divided into coal vertical mill, slag vertical mill and cement vertical mill according to the application. Cement vertical mill is pressurized by hydraulic system, and the pressure acts on the material between the grinding roller and the grinding disc to achieve the purpose of grinding, vertical High grinding efficiency, 20-30% energy saving than ball mill; can simultaneously dry materials with up to 10% moisture; product fineness is easy to adjust; product particle size distribution is uniform; system process is simple; small footprint; low noise Less dust; easy operation and maintenance. With the improvement of vertical grinding technology, it has also been applied in the fields of medicine and food.
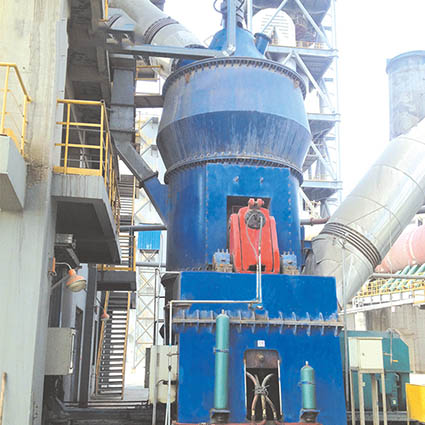
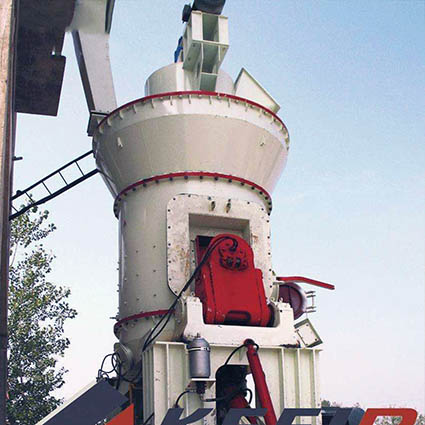
Cement Vertical Mill Structure:
The vertical mill consists of a separator rotation system, a separator part, and an upper casing part upper casing with an inspection door and a feed port, a roller device, a transmission device, a tie rod portion, a disc seal, an upper and lower side, a side friction ring, and an unloading material ring, grinding disc adjusting device, air ring adjusting device, grinding roller pressing system, guide rail protection device, tie rod sealing device, bearing sealing air supply part, inlet oil groove part, internal air pipe sealing, powder selection hydraulic lubrication system.
Techincal Parameter of Cement Vertical Mill
model | Grinding disc diameter (mm) | Roller diameter (mm) | Feeding size (mm) |
Production (t/h) |
Main motor power (Kw) |
Disc rotation speed (r / min) |
Weight (t) |
|
---|---|---|---|---|---|---|---|---|
LM mill |
LM0806 | 800 | 600 | <30 | 3~5 | 75 | 62 | 13. 8 |
LM1311 | 1300 | 1100 | <40 | 9~15 | 200 | 43 | 46. 5 | |
LM1512 | 1500 | 1250 | <40 | 10~19 | 280 | 43 | 65 | |
LM1714 | 1700 | 1400 | <42 | 13~32 | 400 | 40 | 90 | |
LM2215 | 2250 | 1560 | <50 | 25~45 | 800 | 32 | 120 | |
LM2820 | 2800 | 2000 | <65 | 35~80 | 960 | 32 | 200 | |
LM3424 | 3450 | 2400 | <70 | 60 ~100 | 1350 | 30 | 300 | |
LM4831 | 4800 | 3150 | <115 | 95 ~200 | 3150 | 26 | 760 | |
HRM grinding |
HRM1411 | 1400 | 1185 | <35 | 10~15 | 225 | 37. 96 | 49 |
HRM1612 | 1600 | 1200 | <40 | 12~20 | 280 | 36. 16 | 65 | |
HRM1813 | 1800 | 1300 | <45 | 16~28 | 350 | 34 | 78 | |
HRM2115 | 2100 | 1500 | <50 | 20~35 | 400 | 31.6 | 87 | |
HRM2215 | 2250 | 1570 | <60 | 25~35 | 500 | 31P | 92 | |
HRM2417 | 2450 | 1750 | <70 | 28 ~40 | 630 | 29. 5 | 114 | |
HRM2619 | 2650 | 1900 | <75 | 35~55 | 710 | 28. IP | 132 | |
HRM3123 | 3150 | 2300 | <80 | 40 ~80 | 1120 | 25 | 210 | |
HRM3424 | 3450 | 2430 | <80 | 52~85 | 1300 | 24. 5 | 310 | |
HRM3626 | 3600 | 2650 | <80 | 60~100 | 1950 | 24 | 450 | |
HRM4028 | 4000 | 2850 | <90 | 70~115 | 3100 | 22. 9 | 600 | |
HRH4230 | 4250 | 3050 | <100 | 85~160 | 3400 | 22. 18 | 680 | |
HRM4531 | 4500 | 3150 | <110 | 95~200 | 3600 | 21.5 | 750 |
Advantages of Cement Verticle Mill:
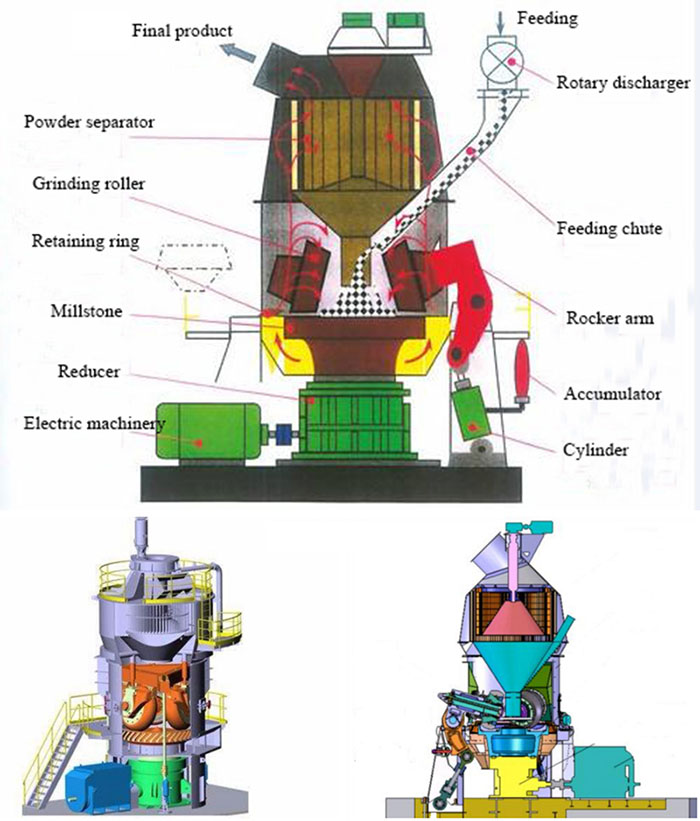
- The vertical milling system has simple process, compact layout and small building area. The floor space is about 70% of the ball mill system. The building space is about 60% of the ball mill system and can be arranged in the open air, which directly reduces the investment cost of the enterprise. And the vertical mill itself has a separator, no need to add a separator and lifting equipment. The dust-laden gas can be collected directly from a bag filter or an electric dust collector.
- The vertical mill uses the principle of material layer to grind the material with low energy consumption. The power consumption of the grinding system is 20% to 30% lower than that of the ball mill, and the power saving effect is more obvious with the increase of the moisture of the raw material. The energy consumption of the vertical mill system is 30% to 40% compared to the ball mill system. Vertical grinding does not have the metal impact of the ball in the ball mill colliding with each other and hitting the liner, so the noise is 20 to 25 dB lower than ball mill. In addition, the vertical mill uses a fully enclosed system, the system works under negative pressure, no dust, and the environment is clean.
- Equipped with automatic control system, it can realize remote control and easy operation. By repairing the oil cylinder and turning the rotating arm, the roller sleeve and liner can be replaced quickly and easily, reducing the downtime of the enterprise.
- The chemical composition of the product is stable and the particle size is uniform, which is beneficial to calcination. The material stays in the vertical mill for only 2 to 3 minutes, while in the ball mill it takes 15 to 20 minutes. Therefore, the chemical composition and fineness of the vertical mill product can be quickly determined and corrected.
- Since the grinding roller and the grinding disc have no direct contact between metals in the vertical grinding operation, the wear is small, and the metal consumption per unit product is generally 5-10 g/t.
Working Principle of Cement Vertical Mill:
The motor drives grinding disc to rotate through reducer, and raw material falls from the feeding port to the center of grinding disc, and hot air enters the grinding chamber from the air inlet. Under the action of centrifugal force, the material moves to the edge of grinding disc, and is crushed by the grinding roller through the annular groove on the grinding disc. Pressed and pulverized, the pulverized material is taken up from the edge of grinding disc by the high-speed airflow of wind ring. The large particles fall directly on the grinding disc and re-grind. When raw material in the airflow passes through the classifier, the coarse powder falls under the action of the rotating rotor. The grinding disc is re-grinded, and the qualified fine powder is ground together with airflow and collected in the dust collecting device, which is final product. The moisture-containing material is dried during contact with the hot air.