Rotary Kiln for Lithium-lon Battery Powder Material
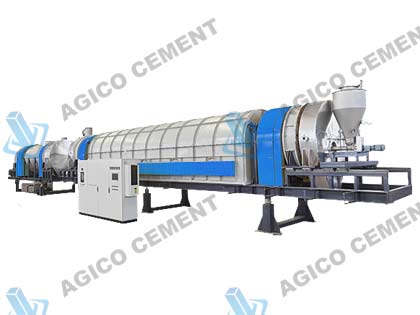
Rotary Kiln For Lithium-Ion Battery
- Rotary Kiln Length: 9m-30m
- Rotary Kiln Width: 800-1600mm
- Temperature Control Accuracy: ±3 ℃ (measured by temperature measuring block)
- Working Temperature: up to 1300℃;
- Heating Resource: Fuel combustion, electric heating,
- Atmosphere Options: Air, O2, N2, C2H2
- Application: Lithium-Ion battery positive and negative electrode material sintering kiln (NCA/NCM second and third firing, SIO negative electrode material)
Lithium-Ion Battery Powder Sintering - Rotary Kiln Specifications:
Specifications mm (Nominal diameter × furnace barrel length) | Rotating speed rpm | Type |
---|---|---|
DN150~300×5000 | 0.5-5.0 | Electric heating rotary cylinder |
DN400~500×6000 | 0.5-4.5 | Electric heating rotary cylinder |
DN600~800×10000 | 0.5-4.0 | Electric heating / gas type rotary cylinder |
DN900~1000×16000 | 0.5-2.5 | Electric heating / gas type rotary cylinder |
DN1100 ~1300×25000 | 0.5-2.0 | Electric heating / gas type rotary cylinder |
DN1400~1500×25000 | 0.5-2.0 | Electric heating / gas type rotary cylinder |
DN1600 ~1800×25000 | 0.5-2.0 | Electric heating / gas type rotary cylinder |
DN2000~2300×24000 | 0.5-2.0 | Electric heating / gas type rotary cylinder |
DN1500~2000,1m3~3m3 | 0.5-5.0 | Electric heating double cone rotary |
Electric Heated Rotary Kiln Structure
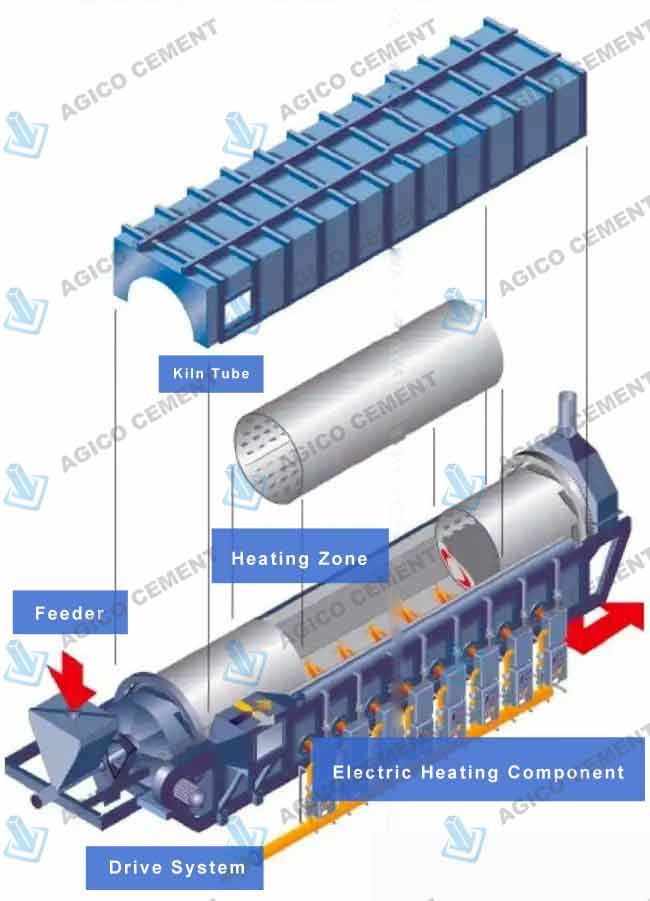
Main Body of the Rotary Kiln
The main body of the calcining rotary kiln consists mainly of the kiln tube, drive system, support device,feeder, inlet and outlet boxes, and other auxiliary components.
Gas Combustion Device or Electric Heating Components
Fuel Burner: The burner uses a diffusion combustion type with forced air blowing, and the flame is horizontally flat and fan-shaped. The air excess coefficient is 1.05 to 1.1%. The air adjustment method uses a double-sleeve air regulator with a gear and rack adjustment mechanism. The burner also includes accessories such as a pilot light, flame monitor, and electronic ignition gun.
Electric Heating Components: silicon carbide rods and molybdenum disilicide rods to generate heat.
Rotary Kiln Body and Insulation System
- For convenient transportation and installation, the rotary kiln body can be divided into multiple sections, made into a wagon-style structure. The rotary kiln is fully assembled at the manufacturer's site and welded together at the user's site.
- The dynamic seal between the cylinder and the rotary kiln wall uses a baffle-type seal, with materials made of high alumina fiber, carbon fiber, and high silica fiber.
- The rotary kiln heating chamber can be divided into multiple heating zones, with adjacent zones separated by partition walls to allow independent heating and temperature control for each zone.
- The rotary kiln bottom uses ceramic fiber modules for insulation.
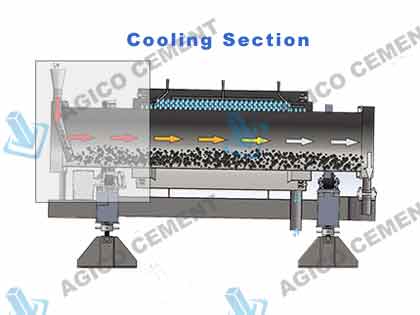
Cooling System
Cooling System of Rotary Kiln
After completing the entire sintering process, the anode and cathode material enters the cooling kiln for cooling, when its temperature is lowered to under 120℃, then it is ready to be discharged from the rotary kiln system. The reactive gases are introduced from the feeding end, and after fully mixing and reacting with the material, they are discharged, dust generated during the production is collected with bag filter.
If you want to know more about Lithium-Ion Battery Powder Material Sintering, Please contact AGICO now for professional Solutions!
Rotary Kiln Customized by AGICO
After customization, Rotary Kiln is used as an important equipment manufactured for lithium-lon battery anode and cathode materials sintering is belonged to the External Heated Rotary Kiln Type, or Indirect Heated Rotary Kiln. It ensure that the cathode materials have a certain degree of crystallinity and particle size.
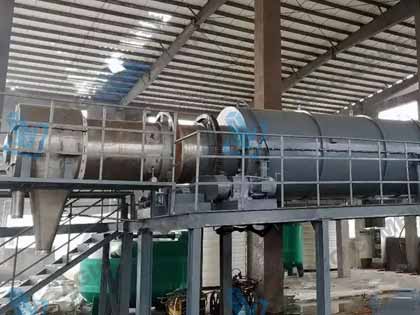
Electric Heated Rotary Kiln Install
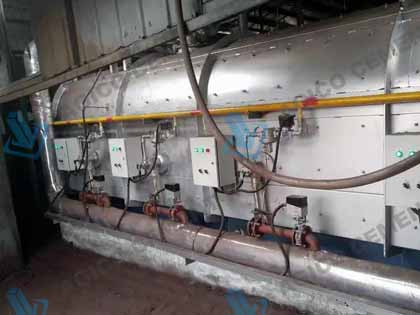
Electric Heated Rotary Kiln In Production
AGICO supplies different rotary kiln heating source solutions for lithium-lon battery powder material, such as coal, gas, oil fuel and electric heated rotary kilns, customers can choose according to their most profitable fuel type.
Features of Electric Heating and Gas-Fired Rotary Calcining Kilns
Electric Heating Rotary Calciner:
- Optimal Sealing: Ensures minimal leakage and retains heat efficiently.
- <Advanced Automation: Incorporates automatic controls and segmented temperature settings for sintering, enhancing operational precision.
- Safety and Reliability: The heating system is designed for safe and dependable operation.
- <Energy Efficiency: Exhibits a surface temperature of the thermal insulation furnace below 65℃, indicative of minimal heat loss, thus proving it to be energy-efficient.
- Compact and Lightweight Design: Features a streamlined structure that is both space-saving and easy to handle.
- <Environment-Friendly: Operates efficiently without contributing to pollution, exemplifying a green technology.
- Operator Convenience: Offers a low-operating intensity and a favorable working environment.
- Maintenance Simplicity: When compared to other energy roasting furnaces, it has simpler auxiliary equipment that is easier to maintain.
Gas-Fired High-Temperature Rotary Calcining Kiln:
- Effective Sealing: Minimizes material and heat loss, optimizing efficiency.
- High Thermal Efficiency: Achieved through the complete combustion of gas, maximizing energy utilization.
- Automated Temperature Control: Features automatic and segmented temperature control for precise thermal management.
- strong>Reliability in Power Outages: Equipped with a system designed to protect against unexpected power failures.
- Superior Thermal Insulation: Reduces heat loss significantly, contributing to overall efficiency.
- Safe Combustion Control System: Ensures the safety and reliability of the combustion process.<
- Compact and On-Site Assembly: Offers a space-saving design with the convenience of on-site furnace body assembly.
- Environmental Advantage: Generates lesser environmental pollutants compared to solid and liquid fuels, promoting cleaner production.
Lithium Battery Material Sintering Process- Rotary Kiln
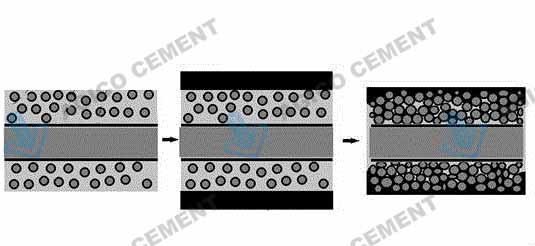
- Preprocess: After the raw materials of cathode materials mixing, grinding, granulated, it will be delivered to rotary kiln.
- Roasting: Rotary kiln reaches certain temperature, cathode materials will go through chemical reactions ( pyrolysis and crystallization reactions), it forms the basic structure of the cathode material.
- Sintering: cathode materials are heated for the sencond time to fuse together and form a dense particle structure.