Ready Mix Concrete Plant
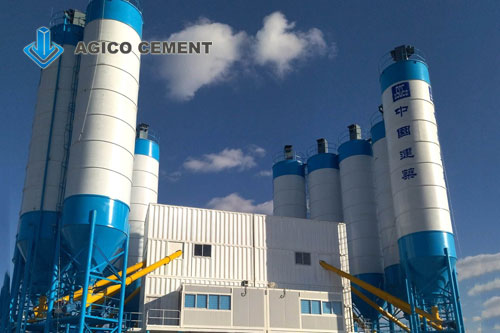
Ready Mix Concrete Plant Details:
- Concrete Plant Type: Stationary Concrete Batching Plant, Mobile Concrete Batching Plant
- Application: Standard Engineering Plant, Environmentally Friendly Plant, Special Concrete Production Plant (Water Conservancy and High-Speed Railway Project)
- Capacity: 25-180 m3/h
- After-Sale Service: Erection & commissioning, operator training
Choose Ready Mix Concrete Plant Types According to Conveyor Equipment
Technical Parameters Of Hopper Type Ready Mix Concrete Plant
Model | HZS25 | HZS35 | HZS50 | HZS75 |
Capacity | 25m3/h | 35m3/h | 50m3/h | 75m3/h |
Mixing system | Twin-shaft concrete mixer | |||
Aggregate feeder | Bucket (Skip hopper) | |||
Discharging height | 1500-3800mm | 3800mm | 3800mm | |
After-sale service | Erection & commissioning, operator training | |||
Warranty | 12 months after erection | |||
Concrete mixer | JS500 | JS750 | JS1000 | JS1500 |
Discharging volume | 500L | 750L | 1000L | 1500L |
Charging volume | 800L | 1200L | 1600L | 2400L |
Mixing cycle | 72s | 72s | 72s | 72s |
Max. mixing size | 80/60mm | 80/60mm | 80/60mm | 80/60mm |
Aggregate batching machine | PLD800 | PLD1200 | PLD1600 | PLD2400 |
Storage bins quantity | 2 or 3 or 4 sorts | 3 or 4 sorts | 3 or 4 sorts | 3 or 4 sorts |
Aggregate scale hopper | 800L | 1200L | 1600L | 2400L |
Technical Parameters Of Belt Type Ready Mix Concrete Plant
Model | HZS60 | HZS90 | HZS120 | HZS180 |
Capacity | 60m3/h | 90m3/h | 120m3/h | 180m3/h |
Mixing system | Twin-shaft concrete mixer | |||
Discharging height | 3900mm | 3900mm | 3900mm | 4000mm |
After-sale service | Erection & commissioning, operator training | |||
Warranty | 12 months after erection | |||
Concrete mixer | JS1000 | JS1500 | JS2000 | JS3000 |
Discharging volume | 1000L | 1500L | 2000L | 3000L |
Mixing cycle | 60S | 60s | 60s | 60s |
Max. mixing size | 100/80mm | 100/80mm | 100/80mm | 120/80mm |
Aggregate batching machine | PLD1600 | PLD2400 | PLD3200 | PLD4800 |
Storage bins quantity | 2 or 3 or 4 sorts | 3 or 4 sorts | 3 or 4 or 5 or 6 sorts | 3 or 4 or 5 or 6 sorts |
Aggregate feeding to mixer by | Belt conveyor |
What Is Ready Mix Concrete Plant
A ready-mix concrete plant (RMC) is a commercial concrete batching plant. It is fully designed to complete the concrete batching process of different standards. The RMC plant’s main function is to batch and mix cement, stone, water, and admixtures into concrete for sale or engineering purposes. AGICO offers 2 ready-mix solutions for stationary and mobile concrete batching plants: hopper feeding and belt conveyor.
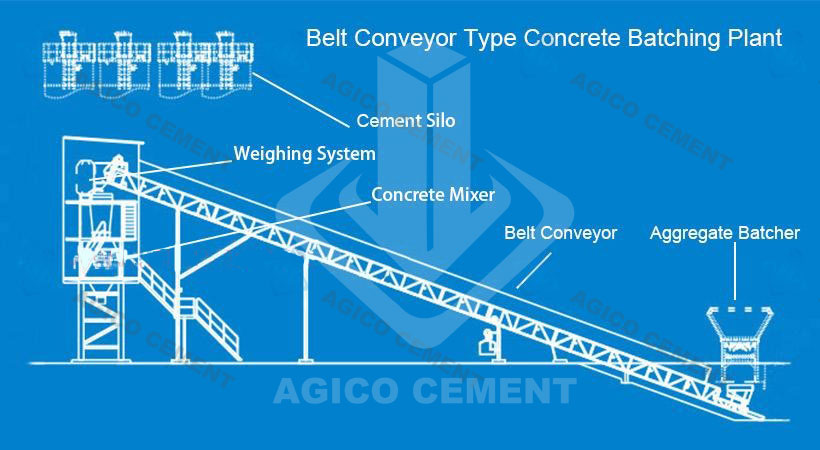
Mobile Concrete Batching Plant: portable type of concrete mixing equipment mounted on wheels, which can be moved to other locations easily. It integrates the function parts of material storage, weighing, conveying, mixing and unloading, along with an automatic control system.
Why Ready Mix Concrete (RMC) Plant is a Better Choice?
Ready Mix Concrete Plant is known for RMC plant in short, Ready-mixed concrete refers to the concrete product pre-mixed in a batching plant. It follows a certain proportion of a specific concrete standard and a specific mix design and is transported to the construction site by a concrete truck after production. It is a common choice for concrete high-quality output. Compared with on-site mixed concrete batching plants, it has better precise batching and mixing control of the raw materials.
How RMC is Delivered
RMC is known for its durability and sustainability and is typically delivered in the following 2 ways:
- Volumetric concrete mixer: Ready-mixed concrete will be delivered to the construction site, allowing you to mix the concrete on-site.
- Bucket Truck or Mixer Truck: The prepared concrete is delivered to the construction site via a mixer equipment mounted on a truck. This type of concrete is recommended as it guarantees higher durability and sustainability.
Why Choose AGICO
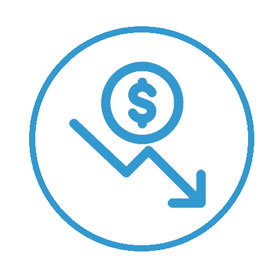
1. Higher Stability and Lower Cost
- Self-developed processing machine tools have the advantages of high precision, easy maintenance, extended life, and reduced noise;
- Intelligent automatic welding robot ensures firmness and beauty, avoiding problems such as slag inclusion, welding leakage, and porosity;
- The structural parts are durable for 10 years and the equipment adopts branded purchased parts.
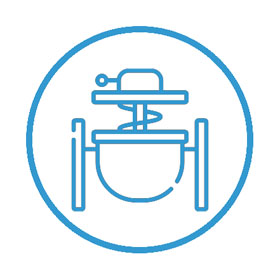
2. High Efficient Mixing System
- Adopt high wear-resistant lining plates and blades with chromium content >26%, and the mixing barrel and blades are 5mm thicker than those in the same industry;
- Multi-arm design shortens mixing time by 15% and provides higher uniformity;
- 6-fold shaft end seal, a spray device is designed above the stirring pump to reduce dust and prevent shaft sticking.

3. Advanced Batching System
- Highly wear-resistant thickened panel and large storage hopper design reduce the number of times the loader loads materials;
- The patented double-bracket machine tool has high precision, easy installation, extended service life and reduced noise;
- "2+2" and "2+3" type racks, quick installation and transfer, split upper and lower warehouses for loading on both sides.
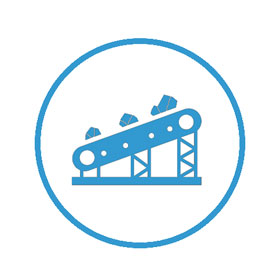
4. Stable Conveying System
- The replaceable friction plate rubber-coated roller greatly shortens the maintenance time and can be replaced in half an hour ;
- 5-times cleaning + water washing, reducing belt loss, energy saving, no noise, maintenance-free and accurate measurement;
- Combined frame structure, standard and energy-saving design, environmental protection and energy saving.
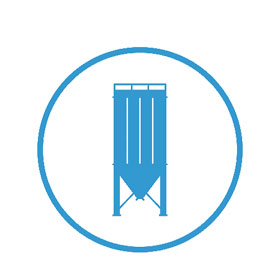
5. Dust Removal and Noise Reduction Design
- The main building uses a large dust collector to remove dust from the main engine and the intermediate warehouse at the same time ;
- The dust removal method has changed from passive dust removal to active dust removal, and from single host dust removal to comprehensive dust removal ;
- The powder bin adopts pulse dust collector with high efficiency ;
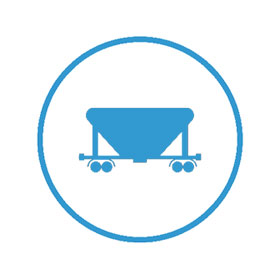
6. Precise Weighing System
- Patented weighing appearance design, larger capacity and easy installation;
- Independent admixture scale, which can realize the "pre-addition method" and "post-addition method" of admixture;
- Accurate measurement, intelligent inching replenishment according to flow rate and intelligent deduction weighing function to ensure the accuracy of ingredient batching.
RMC Plants For Sale
Engineering RMC Concrete Batching Plant
AGICO engineering concrete batching plant can produce various types of concrete, including plastic and dry concrete, mixing mortar, shotcrete, and more. With decades of research and development, it can be tailored to suit your specific site and requirements. AGICO offers you reliable and cost-effective engineering concrete batching plant equipment.
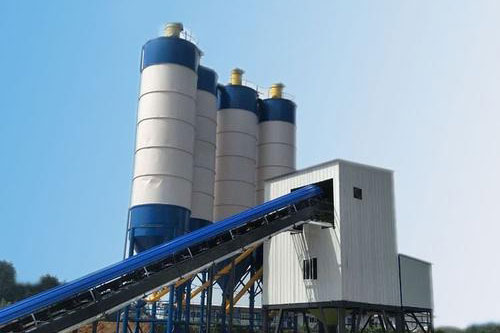
- Hopper loading for small site area, belt conveyor for large output.
- Tailored configuration according to installation method, location area size and customer budget.
- All purchased parts are from brand manufacturers, stable and reliable;
- Multiple dust removal designs, which benefit environmental protection.
- Modular design, convenient and fast transportation, the main body can be installed in 2 days;
- Special space truss structure, good overall rigidity and strong bearing capacity;
- High yield and energy saving, large discharge bin, low loading height, and low fuel consumption of loader;
Environmentally Friendly RMC Plant
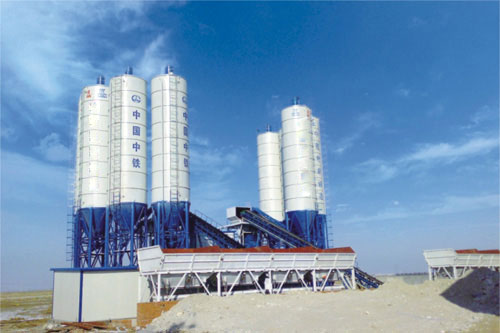
Full Dust Removal And Noise Reduction Design
Fully encapsulated - the mixing main building and silo
The concrete batching machine and material yard are sealed and encapsulated uniformly. Advanced dust removal design - all-around and efficient dust removal for the material yard, belt conveyor, main building and powder silo. Indoor dust emission <5mg/m³; outdoor dust emission <1mg/m3.
Comprehensive noise reduction treatment - use low-noise equipment and optimize design solutions. Daytime noise is less than 60dB, and nighttime noise is less than 50 dB.
Water Conservancy and High-Speed Rail RMC Plant

Special Concrete Production
The high-speed railway project concrete batching plant of AGICO adopts high-precision parent-child screw and a special centralized control system, which first weighs cement and then accurately calculates the proportion of other materials, achieving "0 error" in cement weighing and ensuring that the quality of concrete meets the needs of high-speed railways.
Our Ability
AGICO has cooperated with China Railway Construction Corporation, China Railway Group and other companies on many large projects and is a high-quality supplier of their procurement platforms.
FAQ of Ready-mixed Concrete Plant
Q1: How is the quality of concrete produced using a ready-mixed concrete plant?
A1: The advanced equipment and consistent methods in ready-mixed concrete batching produce a precise, high-quality final product.
Q2: What is the benefit of using automation in a ready-mixed concrete plant?
A2: Automated production requires less human labor, eliminates human error, and helps save on production costs.
Q3: Is the ready-mixed concrete plant environmentally friendly?
A3: Ready-mixed concrete consumes less petrol and diesel, reducing air and noise pollution.
Q4: How does the output of a ready-mixed concrete plant compare to on-site plants?
A4: A ready-mixed concrete plant produces approximately nine times more concrete than an on-site plant, producing 30 to 60 cubic meters per hour compared to just 4 to 5 cubic meters.
Q5: How can ready-mixed concrete reduce cement usage?
A5: Better handling and mixing practices, along with admixtures, can reduce cement usage by 10–12%.
Q6: How to monitor the manufacturing process of ready-mixed concrete?
A6: Strict controls on material testing, key practices, and process parameters are implemented during manufacturing.
Q7: Why the ready-mixed concrete is better than on-site mixed concrete?
A7: Ready-mixed concrete is delivered to the site on time and to specification, avoiding delays associated with on-site batching plants.
Q8: What are the space requirements for storing raw materials in ready-mixed concrete production?
A8: Ready-mixed concrete requires only minimal space on-site for storing raw building materials.