Roller Hearth Kiln
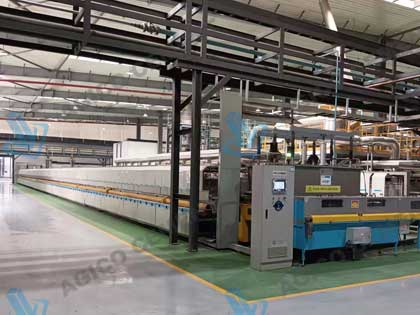
Roller Hearth Kilns for Sale
AGICO supplies customized roller hearth kiln manufacture for customers, funace atmosphere is flexiable, including air, oxygen and N2. There are mainly 4/6 colums and 1/2 layers according to the structure design.
It is primarily used for drying, sintering, and heat treatment processes of lithium-ion battery cathode materials, anode materials, and electrolytes. It consists of a feeding section, preheating section, sintering section, cooling section, and discharging end.
- Excellent atmosphere and temperature distribution Cleaner internal furnace environment
- Cleaner internal furnace environment
- Multiple chambers and extended length can effectively increase production capacity and reduce unit energy consumption
Roller Hearth Kilns for Sale
Roller Hearth Kiln Specifications
Type | Application | Technical Parameters |
---|---|---|
6-Column 2-Layer Nitrogen Roller Hearth Kiln | Sintering of LFP |
Maximum Temperature: 800℃ Furnace Chamber Size: W2280×H400×L68000mm Max Length: 100 m Atmosphere Inside Furnace: N2 |
4-Column 2-Layer Oxygen/Air Roller Hearth Kiln | Sintering of Ternary Materials (NCM, LCO, NCA) |
Maximum Temperature: 1100℃ Furnace Chamber Size: W1520×H200×L50000mm Max Length: 100 m Atmosphere Inside Furnace: O2, Air |
6-Column 2-Layer Oxygen/Air Roller Hearth Kiln | Sintering of Ternary Materials (NCM, LCO, NCA) |
Maximum Temperature: 1100℃ Furnace Chamber Size: W2220×H200×L54000mm Max Length: 100 m Atmosphere Inside Furnace: O2, Air |
4-Column Single-Layer Nitrogen Roller Hearth Kiln | Sintering of Anode Materials (Graphite, Silicon Carbon) |
Maximum Temperature: 1350℃ Furnace Chamber Size: W1520×H250×L60000mm Atmosphere Inside Furnace: N2 |
Rapid Roller Hearth Kiln | Sintering of Magnetic Materials (NiZn) |
Maximum Temperature: 1250℃ Furnace Chamber Size: W850×H150×L8076mm Max Length: 12 m Atmosphere Inside Furnace: Air |
What is Roller Hearth Kiln
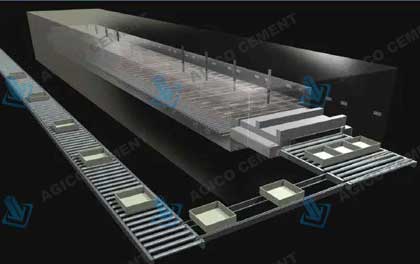
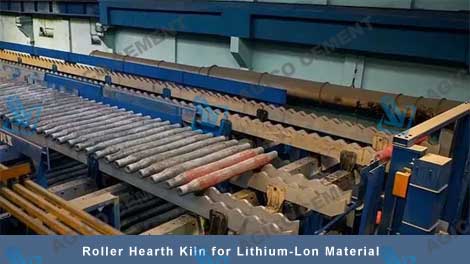
Roller hearth kiln is a type of continous roller hearth furnace for various sintering industry uses. It was once used for sintering of building ceramics, sanitary ceramics, and daily-use ceramics. The New roller material-recrystallized silicon carbide roller increased the temperature to 1200℃ or higher, with upgraded design and manufacture, it is ideal for sintering lithium battery materials, rare earths, magnetic materials, electronic powders, and electrical ceramic parts.
Roller Hearth Kiln Customization - Lithium-lon Material Sintering
Roller hearth kiln can be customized in various aspects, such as temperature control, atmosphere management, material handling. AGICO supplies precise temperature control, advanced atmosphere control system and flex material handling system for tailored solution for supplying high efficiency and quality sintering process, which provide necessary adaptability for different lithium-lon materials.
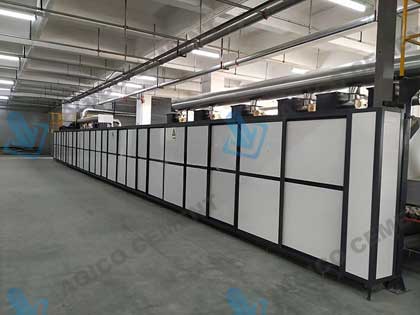
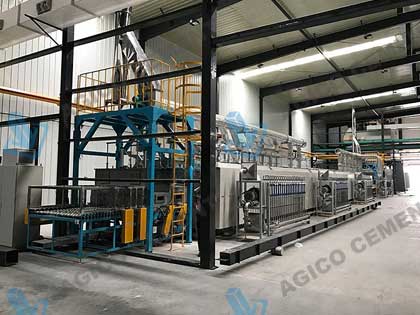
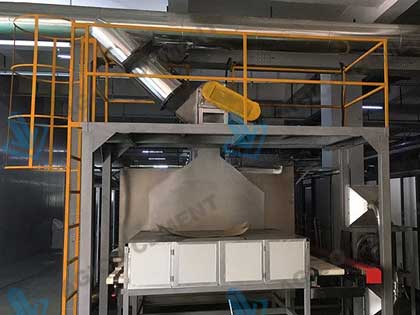
- Adjustable Roller Hearth Kiln Length: according to production capacity requirement.
- Optional Heating Elements: resistance wire or silicon carbon rod
- Wide Temperature Range: 200 ºC -1300ºC
More technical details shall be customized due to the lithium-lon sintering production requirement, feel free to contact AGICO now for professional and accurate answer!
Structure Of Roller Hearth Kiln for Lithium Battery
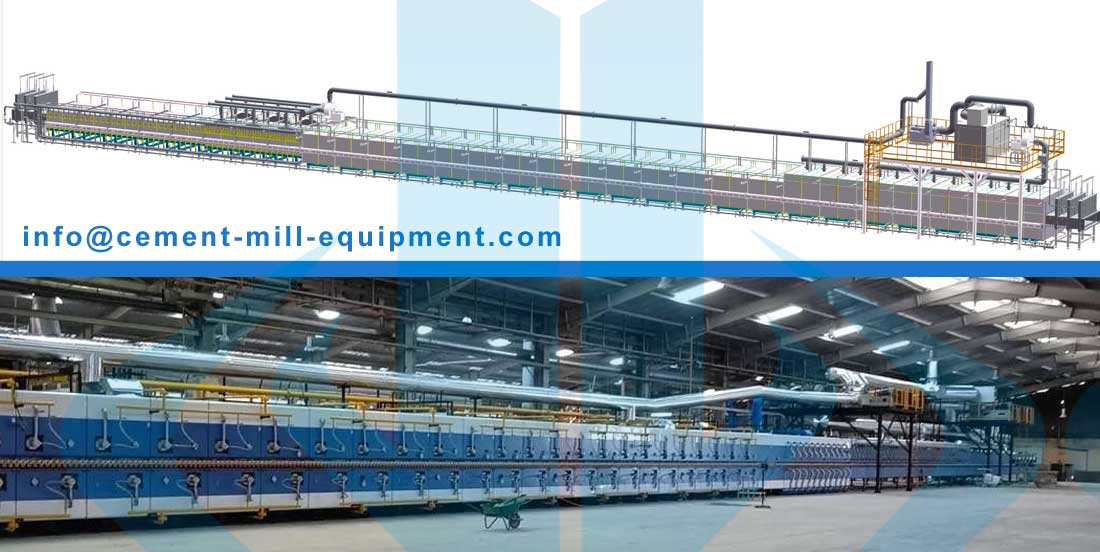
- Feeding Section: Raw materials such as lithium battery cathode and anode materials and electrolytes enter the kiln via a conveyor belt. pre-treat, including screening and weighing are crucial to ensure quality and stability.
- Preheating Section: Raw materials undergo a gradual temperature increase. This section is to remove moisture, volatiles, and other impurities from the raw materials to prepare them for the subsequent sintering process.
- Sintering Section: Raw materials undergo a high-temperature and high-pressure process, which causes the material particles to bond together, forming lithium-ion battery cathode and anode materials with specific mechanical strength and electrochemical properties. The temperature in the sintering section typically ranges from 1000℃ to 1300℃, while the pressure depends on the specific production process.
- Cooling Section: Cool section prevents the raw materials from cracking due to thermal expansion and contraction, and it also enhances the mechanical strength and electrochemical properties of the materials.
- Discharge: Sintered products are conveyed out of the kiln, ready for the next processing step.
Roller Hearth Kiln Applications
The roller hearth kiln is highly suitable for mass production and the processing of a wide range of advanced materials. Its applications include:
- Advanced Ceramic Materials
- Electronic Components
- Powder Metallurgy
- Ultra-Pure Alumina Powder
- Catalysts
- Magnetic Materials
- Rare Earth Oxides
- Alumina
- Zirconium Oxide
- Lithium Battery Materials
- Sodium Battery Materials
- Cobalt Oxide
- Pearlescent Powder
- Ultra-Pure Powder
- Petroleum Catalysts
- Glass Crystallization
- Chemical Powders
- Ceramic Substrates
- Electronic Powder
- Electrical Ceramic Parts
The kiln is used for mass drying and firing processes at working temperatures below 1200°C, making it ideal for a broad spectrum of industries and materials.