800 Mesh Food-Grade Hydrated Lime Production Plant Solution
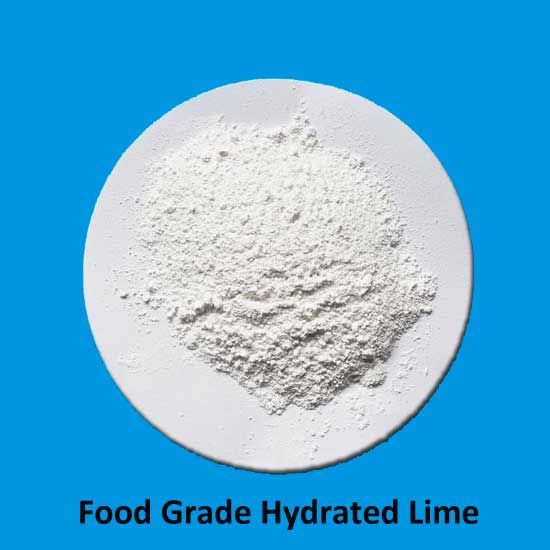
Production Process Of Food-Grade Hydrated Lime
Crushing and Screening: The process begins with transporting limestone ore from the quarry, after which impurities, known as gangue, are removed. The limestone is coarsely crushed using a crusher, screened, and ground with a Raymond mill to produce fine limestone powder. This powder is screened again and combined with pure water to create a suspension. Next, it is filtered through a membrane to eliminate any remaining impurities before being calcined.
Hydration process: Afterward, water is added to form a pulp, filtered at high temperature, flash-evaporated, and dried. The dried material is ground again using a swinging-type Raymond mill. The product is tested to ensure it meets all specifications. Finally, it is sterilized with ultraviolet light before being packaged and stored.
What is food-grade hydrated lime?
According to the national standard GB 25572-2010, the content of food-grade hydrated lime is between 95% and 100.5%, and a limited amount of magnesium and alkali metals, acid-insoluble matter, arsenic, fluoride, lead and other substances is specified.
800 Mesh Food-Grade Hydrated Lime Production Plant

AGICO supplies 800 mesh food-grade hydrated lime production plant. The complete set can produce food-grade hydrated lime powder from 325 mesh to 2 microns (about 6000 mesh). The food-grade hydrated lime production plant includes 3 parts:Quicklime Grinding Equipment,Hydrated Lime Slaking System and Hydrated Lime Ultrafine Vertical Mill.
-
Quicklime Grinding Equipment:
The quicklime grinding equipment is designed to crush and grind quicklime produced by lime kilns. This process transforms the quicklime into a fine powder, which is a preparation for the hydration process. A specialized Raymond mill is a perfect choice, which is economical and affordable.
This traditional mill is a type of coarse grinding equipment. It has a pulse dust collector at its residual air outlet, achieving a dust collection efficiency of 99.9%. Since all positive pressure components of the main machine are sealed, a dust-free processing environment is formed.
The quicklime processing system is efficient and energy-saving, allowing for a larger processing volume and higher efficiency within the same grinding time. Compared to the R-type mill, the output has increased by over 40%, while unit power costs have decreased by more than 30%.
The quicklime grinding machine is a truly efficient and energy-saving equipment. The lime powder produced ranges from 80 mesh to 400 mesh, making it suitable for fast hydration process.
-
Hydrated Lime Slaking System
The hydrated lime slaking system is a large-scale equipment designed to produce industrial-grade and coating-grade hydrated lime (gray calcium powder). A fast and efficient slaking system is essential for high-volume production of 800-mesh food-grade hydrated lime. This system can be customized to meet customer requirements. It offers several advantages:
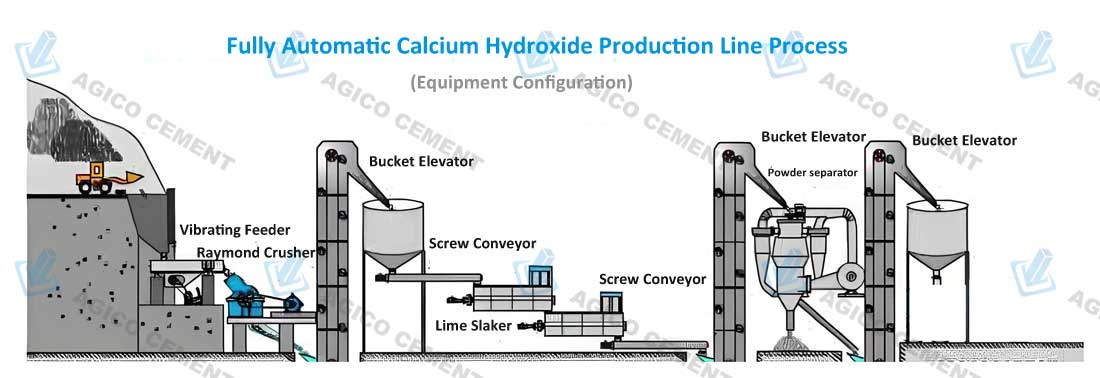
-
Control System
Choose from a variety of configuration modes: 1. Manual control 2. Automatic control 3. Manual + automatic dual control mode 4. Intelligent water distribution system -
Dust Collection
Pulse bag dust collector and water dust removal dual dust removal system. The dust removal efficiency can reach ≤ 5mg/m3, which is more environmentally friendly. -
Slaking System
It has the function of pre-slaking, maintains high temperature and constant temperature digestion, occupies a small area, has a volume that is more than 10% larger than similar domestic equipment, and an effective length that is more than 50% longer than similar domestic equipment, allowing for more complete digestion. -
Pre-hydration System
1. The pre-hydration blade adopts a detachable alloy wear-resistant bushing to achieve long-term wear-free and easy replacement.
2. The optimized single axis is adopted to achieve a uniform dispersion effect of the double axis, reducing the probability of broken blades and broken axes of the double axis.
3. There is no need for manual cleaning during a power outage or abnormal shutdown, which improves the on-site environment. -
Homogenization System
1. Improve the powdering degree of hydrated lime
2. Reduce the temperature of hydrated lime finished product -
Rapid Hot Water Slaking
Using the slaking heat, the system water temperature is heated to about 80°C in 5 minutes, which speeds up the digestion speed and milling rate. -
Hydration Degree
The entire hydration process is 35-40 meters long and takes 100 minutes.
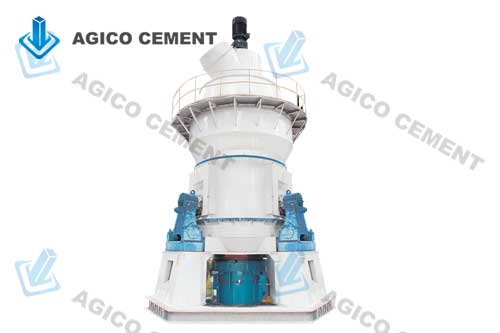
Hydrated Lime Ultrafine Vertical Mill
-
Hydrated Lime Ultrafine Vertical Mill:
The hydrated lime ultrafine vertical mill has a secondary classification system. This system includes ultrafine classifiers, fans, dust collectors, silos, screw conveyors, pipelines, and other equipment, which the ultrafine classifier serves as the core component.
After the ultrafine vertical mill grinds hydrated lime into a powder ranging from 325 mesh to 2500 mesh, it can produce 800 mesh food-grade hydrated lime directly. If customers want to produce a finer food-grade hydrated lime, it can be equipped with a secondary classification system.
The secondary air separation grading system boasts high powder selection efficiency. This system can effectively separate coarse and fine powders, the separation fineness is up to 3 micrometers (μm), so wide ranges of qualified product production can be realized.
Hydrated Lime Production- Dry Process and Wet Process
Hydrated lime dry process
Qualified quicklime is first crushed using a jaw crusher, then transported to the lime silo via a bucket elevator and a bin-type vibrating conveyor. The lime is quantitatively fed into the lime pre-hydrator through a star-shaped feeder. Here, it is initially hydrated with strong agitation from a stirring rod. Then enter the lime slaker system to complete the hydration process.
Once hydration is finished, the processed lime is transferred to the lime silo using a lime elevator and a screw conveyor. The fine-slaked lime is then separated using a spiral air separator, output qualified fine-slaked lime, which is unloaded into a finished lime silo for the package.
Why Choose Dry Process Method? During the dry hydration reaction, the organizational structure of the lime changes, causing Ca(OH)₂ to form a loose powder, which increases in volume to 1.5 to 2.0 times that of the original material. The raw material has excellent fluidity, enabling the dry hydration process to achieve a high conversion rate even with a low water-to-lime mass ratio. This is suitable for large-scale food-level hydrated lime production.
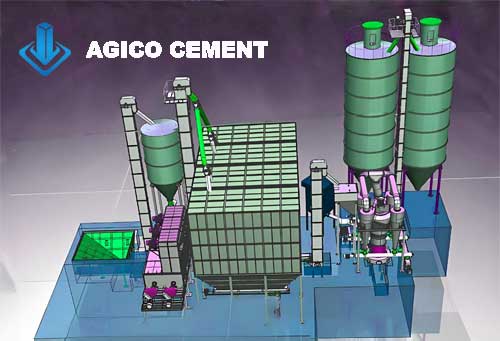
Hydrated lime wet process
After limestone is heated and converted into calcium oxide, it is mixed with water in a specific ratio. Hydrated lime is output in the form of gray calcium powder, It needs to undergo 2 steps to remove impurities: purification and separation. It is then centrifuged, dehydrated, and dried at a relatively high temperature before being screened to produce the final hydrated lime product.
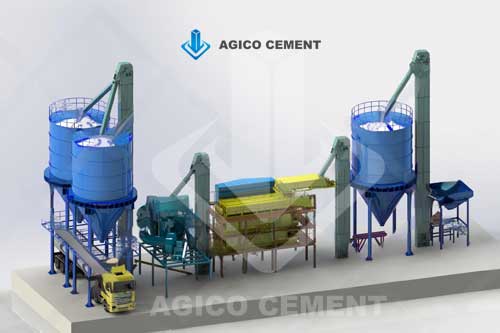
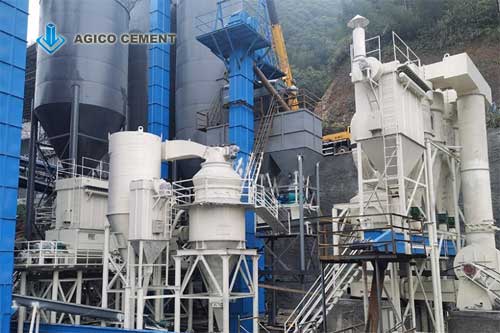
The dry process has the following advantages: low investment costs, a short transformation cycle, straightforward operational steps, and effective treatment results. Its’ product - the high-activity hydrated lime has fine physical properties, such as a large specific surface area, substantial pore volume, high effective calcium content, and a strong ability to capture acidic pollutants.