Raw Mill Grinding Solution
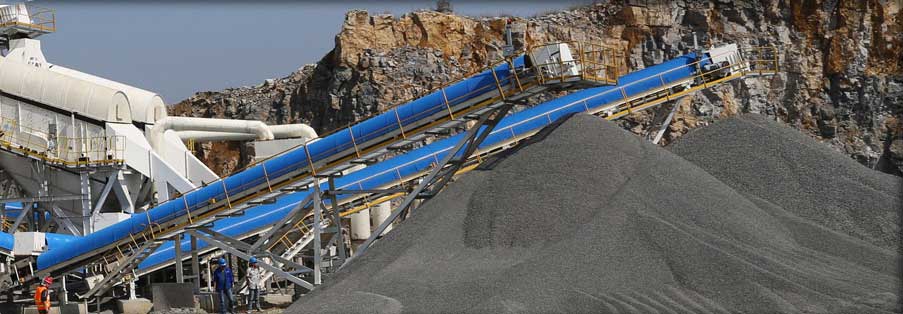
Raw Mill Equipment Introduction
Raw Mill Production Equipment: stone crushing process is composed of vibrating feeder, jaw crusher, impact crusher, vibrating screen, belt conveyor, centralized electric control and other equipment.
Raw Mill Application scope: aggregate.
Sand and stone aggregate refers to sand, stone and other granular materials mixed with cement and water when making mortar or concrete, also known as aggregate. A granular, loose material that acts as a skeleton or filler in concrete. In concrete, sand and stone account for about 3/4 of the total volume of concrete, coarse aggregate and fine aggregate. Coarse aggregate includes pebbles, gravel, waste slag, etc., fine aggregate includes medium fine sand, fly ash, etc.
Raw Mill Processing equipment
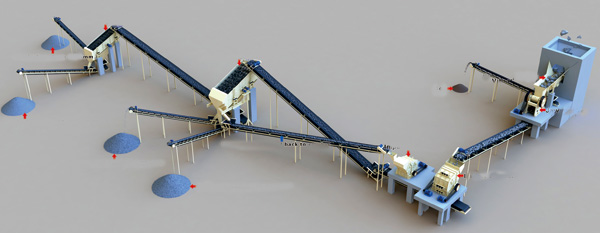
The main equipment of aggregate production line is: primary crushing jaw crusher, secondary crushing impact crusher and cone crusher, followed by impact crusher namely sand making machine, and finally grinding machine. It plays a very important role in the construction class, when mixing materials, cement by water mixing, into a thin paste, if you do not add aggregate, it will not be able to form, will lead to unable to use. So in the construction industry, aggregate is leading a very important role. Sand and stone is an indispensable building material, widely used in construction, roads, highways, railways, engineering and other fields.
Aggregate production line is feeding, crushing, screening, lifting, conveying, dust removal as one of the assembly line operation equipment. Through the reasonable distribution of the crushing ratio of the sand aggregate production line and the optimization of the details, the efficiency of the sand and stone production line can be improved, and the quality of the mechanism sand and stone can be improved.
Processing system
Sand and stone aggregate processing system can be divided into two basic types: artificial aggregate processing system and natural sand and stone processing system. Mainly according to the material source situation near the main project, which form of sand and stone aggregate processing system is selected to establish. For natural aggregate material source is sufficient, and the gradation is more appropriate, natural sand and stone aggregate processing system is generally used. Artificial aggregate processing system is generally used when the natural aggregate source is not sufficient, or the material source is sufficient but the grading difference is large, and the amount of discarded material is large.
The aggregate production line is to feed the crusher through the feeder, break the material in the crusher, and then pass through the conveyor belt to the vibrating screen after sifting out the finished material. In this production process, all the equipment together form the aggregate production line. Our company has been engaged in the mining industry for more than 30 years, and has rich experience in the construction of the aggregate production line. It can undertake the construction of production lines of 500-30,000 tons per day, not only reasonable design, less maintenance costs, durable equipment, has a good user reputation in the mining industry.
Feeding system stone production line
Feeding system stone production line system is to each section of crusher equipment and screening machine to send raw materials, according to the crushing and screening process. The equipment to complete the feeding link is the vibrating feeder or other types of feeding equipment. In the sand and stone production line, the feeding machine is generally used for the supply of stone.
Crushing system
Crushing system Stone production line system is the heart of the whole equipment. Its work is to break all kinds of ore raw materials into finished materials with required particle size. A combined sand and stone production line can be composed of multiple breakers. These crushing mechanical properties are different, together to complete the crushing work of stone.
Stone production system is the crushing after the ore screening machinery for screening. In composite production line, sand and stone need to be separated, and then need to be transported to their respective sites. The equipment used in this process is usually linear vibrating screen or other screening mechanical equipment.
Highlight advantages
The aggregate crushing production line has a high degree of automation, and the whole production line hardly needs manual operation in addition to the startup and shutdown of the equipment and daily maintenance.
Its production efficiency is high, the operation cost is low, the output is large, the income is high, the finished stone particle size is uniform, the grain shape is good, in line with the national high-speed material requirements.
Raw Mill Process flow
First of all, the aggregate is evenly sent to the jaw crusher for preliminary crushing by the feeder, and then the coarse material produced is transported by the conveyor to the impact crusher for further crushing. The fine crushed aggregate is screened out of different specifications by the vibrating screen, and the aggregate that does not meet the size requirements is returned to the impact crusher for crushing again, and finally the required products are reached.
Raw Mill Production Line Specification:
Model | 2ZM-100 | 2ZM-200 | 2ZM-400 | 2ZM-600 | 2ZM-800 | 2ZM-1000 | 2ZM-1200 | 3ZM-2000L |
Roller number | 2 | 2 | 2 | 2 | 2 | 2 | 2 | 3 |
Roller Volume(L) |
100 | 200 | 400 | 600 | 800 | 1000 | 1200 | 2000 |
Grinding way | Dry ,wet ,open and close barite grinding mill | |||||||
Feeding size (mm) |
0-25 | |||||||
Discharging size(mm) | 0.3-0.074 | |||||||
Amplitude (mm) | 10-14 | 10-14 | 8-13 | 7-9 | 7-9 | 7-9 | 7-9 | 7-9 |
Vibration frequency (r/min) |
980 | 980 | 980 | 980 | 980 | 980 | 980 | 980 |
Capacity(t/h) | 0.6-1.3 | 0.75-2.5 | 0.8-4.8 | 1-8 | 1-10 | 1-10 | 1-16 | 1-40 |
Motor power (kw) |
17-22 | 22-37 | 45-55 | 45 | 55-75 | 75 | 75-90 | 135 |
Size(L*W*H)M | 2.5*0.85*1.5 | 2.8*1*1.8 | 3.2*1.1*1.9 | 3.4*1.5*2.2 | 3.4*1.6*2.2 | 3.8*1.6*2.3 | 5*1.7*2.5 | 7*1.7*2.35 |
Weight(t) | 2.6 | 3.5 | 4.8 | 6.2 | 9.2 | 11 | 14 | 20 |