Sintering Kiln For Lithium-lon
Lithium-lon Battery Material Sintering Kiln Types:
The lithium battery material sintering kiln (calcining kiln) is a lightweight continuous industrial kiln, which is used for the rapid firing of ternary positive and negative electrode materials. For continuous sintering production, there are 3 main product types: Roller Hearth Kiln, Pusher Kiln and Rotary Kiln.
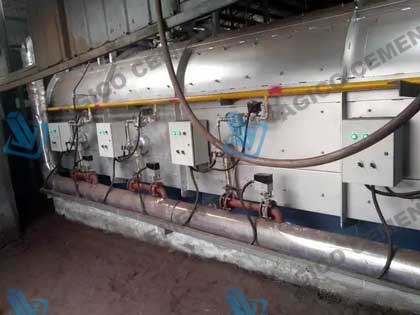
Rotary Kiln
The rotary kiln has higher energy consumption. With the advantages of low temperature, short firing cycle, good furnace temperature uniformity, and low labor intensity.
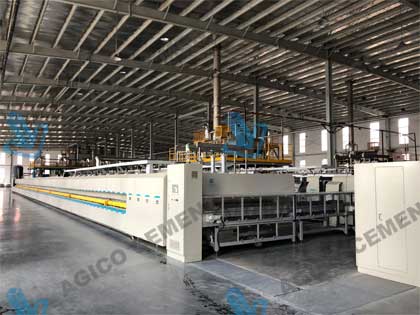
Roller Hearth Kiln:
The roller hearth kiln is a kiln equipment for firing lithium battery powder materials. It can be used for sintering powder materials in an oxidizing atmosphere.
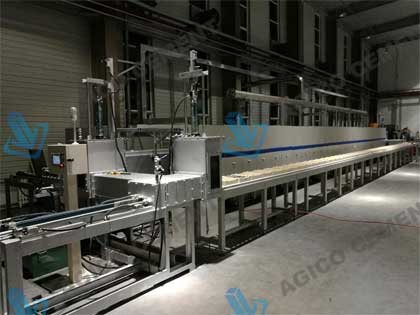
Pusher Kiln
The pusher kiln for lithium batteries is specialized equipment used for high-temperature processing in the production of lithium battery materials.
Lithium-lon Battery Anode and Cathode Material Sintering Solution
The positive electrode materials of lithium batteries consist of compounds such as lithium cobalt oxide, lithium nickel oxide, and lithium manganese oxide, while the negative electrode materials are mainly graphite and silicon-based materials. The sintering process for Lithium-lon Battery material include cathode and anode materials, which varies due to their distinct material compositions and requirements:
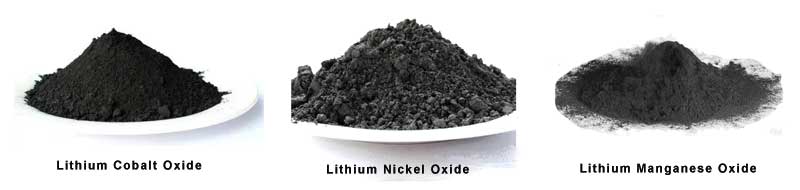
Cathode Material Sintering
The sintering of cathode materials in lithium-ion batteries generally demands high-temperature conditions ranging from 700°C to 1000°C. This process is crucial to achieving the desired material characteristics, such as enhanced electrical conductivity and structural integrity. Sintering in an oxygen-rich atmosphere is vital for these materials, often requiring furnaces equipment capable of providing and maintaining such conditions.
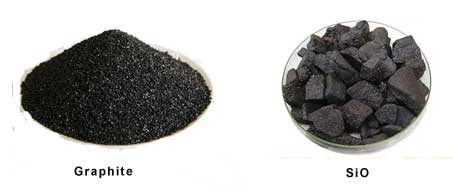
Anode Material Sintering
Anode materials undergo sintering at even higher temperatures, between 950°C to 1100°C, and in a radically different atmosphere—hydrogen gas or nitrogen gas. These gases provide protective and stable environment that is essential for preventing oxidation of graphite or silicon-based materials. The anode materials sintering also necessitates specialized containers and atmospheres. Graphite environments are commonly employed due to their ability to endure high temperatures under atmospheric protection.
Rotary Kiln for Lithium-lon Battery Powder Material
Rotary Kiln Length: 9m-30m Rotary Kiln Width: 800-1600mm Temperature Control Accuracy: 3 ℃ (measured by temperature measuring block) Working Temperature: up to 1300℃; Heating Resource: Fuel combustion, electric heating, Atmosphere Optio...
Read MorePusher Kiln
High temperature control accuracy Large production capacity Low energy consumption High product yield Reliable operatio Usage : Firing of alumina, zirconia, and electronic ceramics Maximum temperature : 1650℃ Furnace cavity size : W850H39...
Read MoreRoller Hearth Kiln
Roller Hearth Kilns for Sale AGICO supplies customized roller hearth kiln manufacture for customers, funace atmosphere is flexiable, including air, oxygen and N2. There are mainly 4/6 colums and 1/2 layers according to the design. It is pri...
Read More