What Factors can Influence Rotary Kiln Burner Working Efficiency
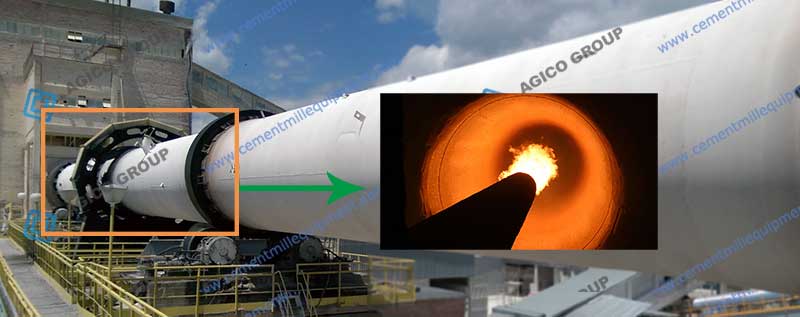
The main factors affecting the shape of the rotary kiln burner flame and working efficiency include 2 main parts: the combustion velocity of pulverized coal and the velocity of airflow in the rotary kiln. AGICO Cement list the factors as follows:
Pulverized Coal Quality and its Dosage
Pulverized coal volatiles: pulverized coal with low volatiles (< 15%) tends to form rotary kiln burner flames with long black heads, short high temperature parts and high local flame temperatures. Although the coal powder with high volatiles (> 30%) is quick to ignite, it takes a certain time for volatiles fractionation and combustion, and the gas layer on the coke particle surface is thick, so the oxygen around the coke is not much when it starts to burn, so it forms a longer flame near the kiln head with a slightly lower temperature and a higher temperature.
Item | High-temperature Gas Recirculation Burner | Conventional Burner |
---|---|---|
Combustion system | Recirculating flow is formed in the burner to promote the release of volatile matter of pulverized coal. Subsequently, combustion is made by internal recirculating flow by means of secondary air. |
Combustion is made by charging pulverized coal into the internal recirculating flow by means of secondary air. |
Features |
· Recirculation of high-temperature gas by involving · Recirculation by turning flow · Higher temperature of primary air · Partial premixing · Control of high-temperature gas recirculation flow of tertiary air |
· Recirculation by turning flow · Strong mixing |
Ash content of pulverized coal: when ash content of pulverized coal increases, calorific value decreases, combustion speed slows down, flame elongation and temperature decreases.
Water content of pulverized coal: When water content increases, flame temperature decreases and black flame head elongates.
The amount of coal: the greater the coal concentration in the primary air, the longer the time of mixing coal powder with the primary and secondary air, and the longer the duration of combustion. Therefore, when the primary wind is unchanged and the amount of coal used is increased, the flame will elongate.
Coal Injection Nozzle Position and Shape
Nozzle position: When the secondary air enters the rotary kiln burner, the mixing of the primary and secondary air is weak, which extends the burning time and makes the flame extend. For example, before the secondary air enters the kiln, the mixing between the primary and secondary air will be strengthened to shorten the flame.
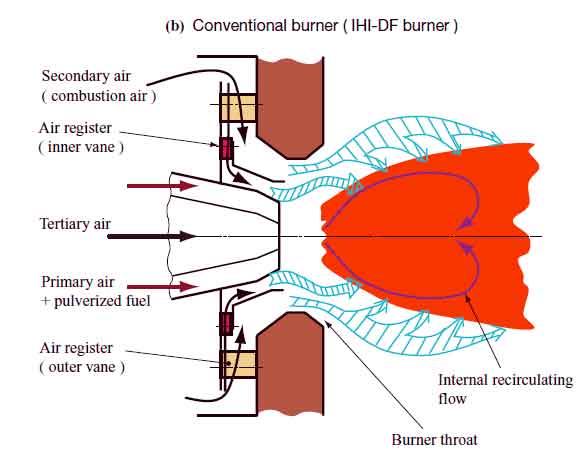
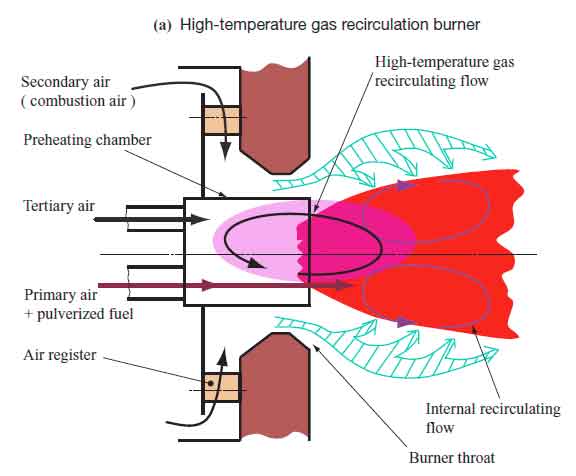
Coal nozzle shape: the air coal outlet speed of the straight nozzle is small, so the coal powder range is close, the flame is thick. The air coal outlet speed of the drawing pin nozzle is large, the coal powder has a long range and the flame is concentrated. The flame ejected after the coal injection pipe is equipped with wind wings is shorter and more concentrated than when the wind wings are not installed.
Primary Wind Air Volume and Speed
Air volume: for coal with high volatile content, one more air should be used; Otherwise, the volatiles will not burn quickly and the rotary kiln burner flame will be stretched and cooled. For low volatile coal, less use of a wind, otherwise coal ignition will be delayed, and easy to cause local high temperature.
Wind speed: if coal has high volatilize cent and low ash content low, a wind speed can be bigger, so can accelerate combustion speed, improve the flame temperature. For coal with low volatilization, the velocity of primary wind should be lower to avoid the elongation of black flame head and the high temperature part.
Air temperature: If the primary air temperature is high, the coal powder is preheated, and the black flame is short. When the coal volatilization is low, the primary air temperature should be controlled higher to speed up the ignition of coal powder and shorten the black flame.
Kiln Tail Exhaust and Secondary Air
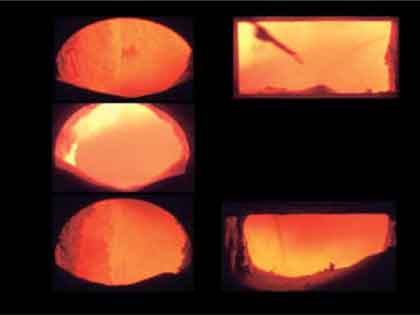
When the rotary kiln tail exhaust air is constant, the primary wind increases and the secondary wind decreases. When the primary air volume is unchanged, the exhaust air at the rotary kiln end increases, and so is the secondary air. When the primary air and coal consumption are unchanged, if the exhaust air is increased, the excess air will increase and the rotary kiln burner flame temperature will decrease.
When the primary wind is unchanged and the amount of exhaust air and coal used is increased, while the same amount of excess air is maintained, the concentration of pulverized coal in the primary wind increases, the flame becomes longer, but the temperature decreases. If the secondary air preheating temperature is increased, the flame temperature can be increased and the black flame head can be shortened.
Main Test Conditions
Fuel | Unit |
Coal A ( anthracite ) |
Coal B ( semi-anthracite ) |
Oil coke |
---|---|---|---|---|
Combustion rate | t/h | 1.2 | 1.2 | 1.2 |
Exhaust gas O2 | % | 3.5 | 3.5 | 3.5 |
Staging air ratio | % | 0 - 30 | 0 - 30 | 0 - 30 |
Temperature, Raw Materials and Air Volume in Rotary Kiln
The temperature in the rotary kiln is low, even if there is enough air, the pulverized coal cannot be completely burned. When the raw material is thick or close to the rotary kiln head, the flame should be shortened. If there is too much excess air in the kiln, the rotary kiln burner flame temperature will be lowered.
Material Composition
When the material composition in the rotary kiln is reasonable, cement clinker granulation is fine and even, with flexible tumbling, good flame shape and high temperature. If the composition is unreasonable, such as liquid amount is too much, then the firing range will become narrow, easy to bulk, and lead to limitation of the flame temperature rise, or easy to ring, flame shorten.