Roller Press Install For Pre-Grinding Before Cement Ball Mill
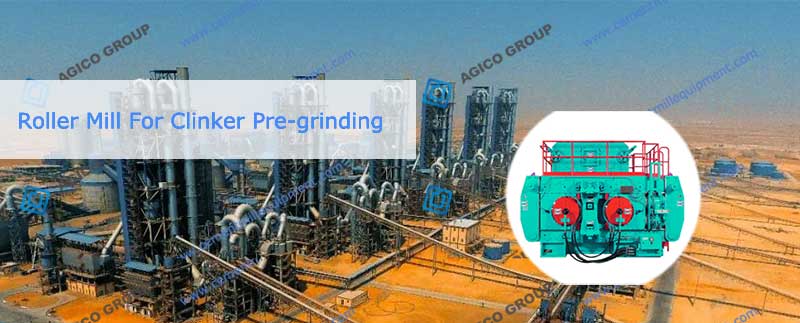
The design of set high efficiency big capacity of cement roller press (or vertical mill) and air classification equipment before ball mill, helps realize the seperate grinding "section", this makes the grinding processes more controllable, after preprocessing classification,clinker delivered into the grinding materials have a combination of "size effect and crack effect", which significantly improved the grinding effect of raw material, and helped a lot in increasing production, and reducing energy cost in grinding system.
Roller Press Steel Structure Frame Specification:
Type of cross section used (C.S) | Overall length of member (L) | Plate Thickness (T) | Plate Hight (H) | Plate Material | Material Standard | Material Yeild Strength (YS) |
---|---|---|---|---|---|---|
Solid rectangular cross section | 7597 mm | 255 mm | 630 mm | Non alloyed structural steel (In hot rolled condition) | EN 10025-2 | 265 MPa |
Why install Roller Press in Cement Manufacturing Plant
The overall trend is to increase the capacity of pre-grinding bed, and transfer 60% to 70% of of the ball mill functions section to it and high fine airflow classification equipment to complete the system, with a large range of increased production and power saving capacity. For example, the particle sizes of the grinding materials can be less than 200 μm or even less than 100 μm in the two-stage high-fine airflow classification process in the combination of dynamic and static. Relative to cement ball mill, crushing the storehouse of all functions and most of the fine grinding storehouse function has moved to pre-grinding section, ball mill is concentrated on finish grinding fine cement particles and plastic, pre-grinding section of the output, the more the system block the clearer, the greater the increase production, (about 100% ~ 200% or higher), the more significant the grinding power consumption (power saving 20% ~ 30%).
Brief Introduction of Roller Press in Cement Grinding Unit
As is known to all, the cement prepared by ball mill grinding mechanism has high sphericity and good performance. However, due to the treatment of clinker inside ball milling machine, it can only rely on the "cluster grinding effect" of the grinding balls to do random work. The grinding efficiency of one bin is low, and the power consumption of the grinding section is high. As a high pressure "material bed grinding" cement roller press (or vertical mill), grinding efficiency is more than 2 ~ 3 times higher than ball mill.
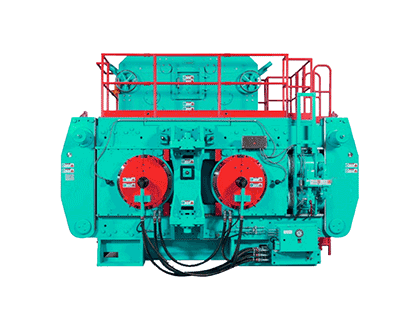
In application of roller press in cement grinding line, although the preparation of the finished product temperature and grinding system power consumption is low, considering the influence of finished product of cement particle morphology, such as setting time, water requirement of normal consistency index of performance and durability of concrete construction, the current domestic temporarily choose not to use cement roller press in grinding system, but now the domestic existing cement vertical mill grinding system run more than 100 sets cement mill plants.
All cement design institute in the design of cement grinding unit, according to owner's actual demand and the present situation of the local mixed material resources, adopt different processing capacity of cement roller pressure before grinding machine (or vertical mill) pre-grinding material bed with different grading equipment configuration, and ball mill unit into open joint (or half) grinding system, or with the finished product joint (or end) classifier composed of double closed loop grinding system. However, in these grinding systems, when ball mill size is unchanged, the grinding system output is different from the grinding power consumption according to the size of the pre-grinding equipment configured ahead of the ball mill.
Cement Grinding Unit Working Efficiency
Cement grinding is a continuous process in which the particle size of clinker is continuously ground and reduced, until it meets the qualified requirements by means of mechanical and chemical activation, and utilizing the "cluster grinding effect" of the grinding body inside ball mill. Processing capacity of advance material bed before the cement grinding equipment is small, the quantity of fine powder of the grinding material particle size is larger,as ball mill section needs to complete the whole system of 60% or more than 70% of the workload, grinding material cannot be limited within the bed material and low grinding efficiency, little power consumption decreased, there is still a bottleneck of the system output and power saving . The power consumption of cement pulverizing system with small capacity of pre-pulverizing section is still in the low level of 38 kWh/t or even above 40 kWh/t. In a word, the more work done in the ball mill section, the higher the grinding power consumption of cement grinding unit.
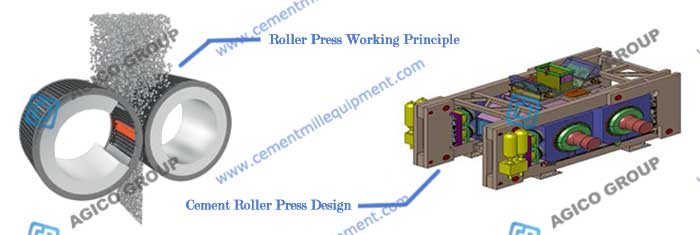
At present, the material bed pre-grinding equipment capacity is bigger, material adopts the high fine classified process joint (or end) of grinding open circuit and closed circuit system, the subsequent ball mill using conventional metal grinding body according to the different materials. Take production of p. O42.5 grade cement as an example, the cement grinding unit power consumption indicators have reached 27 kWh/t, or less 25 kWh/t level or less, sometimes even has reached 23 kWh/t or less.