Power Consumption of Cement Manufacturing Plant
Power Consumption in Cement Manufacturing Plant:
The cement industry, as a traditional high power consumption industry, power consumption in the cement grinding process takes a large ratio in the whole production, electric power consumption is about 60%-70% of the total consumption. With more and more strict Energy conservation and environmental protection policy published, excess production capacity, and severe market competition, energy conservation in cement grinding plant is the key for Cement Manufacturing Plant to achieve the purpose of reducing power consumption. Fuel and electricity costs are the single largest variable production cost at cement mill plants. Variable costs are typically about 50% of overall operating costs, so energy cost is usually the single largest production cost, besides raw materials. Labor cost is relatively a small part of the Cement Manufacturing Plant.
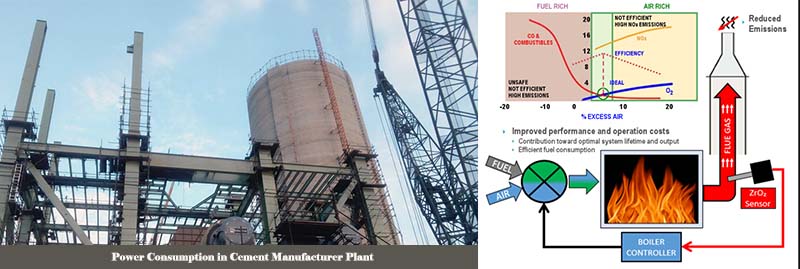
Most of the energy usage is in cement production drives end-use, a lot of power is consumed in the processes of cement grinding, raw material crushing, and materials transport, cement transport. The cement industry natural gas consumption is concentrated in the process of heating end use (about 90% of total gas consumption), which involves clinker production in large kilns. In most cases natural gas is used as a supplemental fuel to coal, natural gas has the advantages of easier delivery, heat control, and there are other fuels can be used in cement rotary kiln, such as biofuels, the only problem is that it might cause pollution with unwanted gas created, or it is not sustainable for a continuous supply.
Nowadays, in the field of cement grinding system of the world cement industry, the major cement grinding equipments include loop flow ball mill, roller press, ball mill semi-finishing system, and vertical mill system, in which ball mill and vertical mill are 2 major cement grinding systems in Cement Manufacturing Plants. Although all kinds of cement grinding plants have their advantages and disadvantages more or less, all kinds of innovation and technological progress are constantly upgrading and updating, and the grinding technology of the cement industry is also developing towards high efficiency and intelligence.
Metal Content in Clinker From Fuels
Metal (in g/t of clinker) | |||
Cadmium | Lead | Zinc | |
Inlet Streams | |||
Waste Oil | 0.0635 | 4.77 | 31.77 |
Coal | 0.0261 | 10.43 | 7.39 |
Raw Meal | 0.31 | 23.25 | 72.85 |
Outlet Streams | |||
Clean Gas | 0.000256 | 0.0152 | 0.058 |
Clinker | 0.399 | 38.43 | 111.94 |
Destruction and Removal Efficiency (%) | 99.94 | 99.96 | 99.95 |
Power Consumption of Cement Manufacturing Plant At Present
At present, the average level of unit energy consumption of Cement Manufacturing Plants is at 33 kWh, in some Cement Manufacturing Plants, it could be 40 kWh higher than the average number. Through technology improvement, equipment update, and new type abrasion materials, the Cement Manufacturing Plant could reduce the unit energy consumption of the grinding process to 20 kWh. For example, the power consumption of Pizhou China United cement grinding has been reduced to 23 degrees per ton, which is big progress has been made. It could save almost 1/3 of the average electricity consumption.
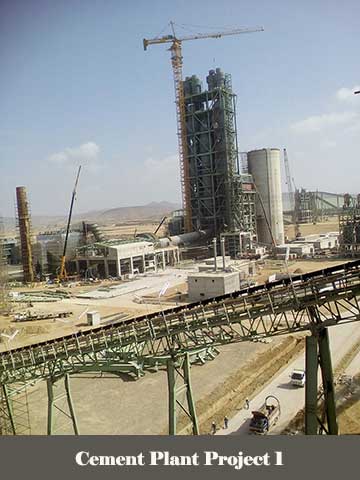
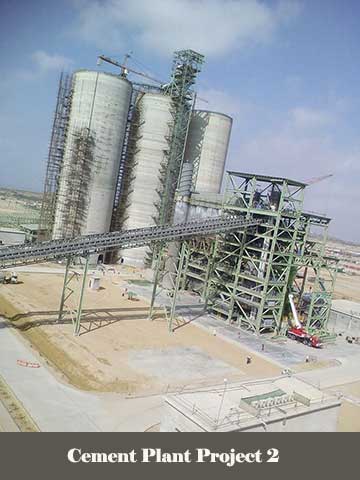
The technical center of the Henan operation area of China United Cement Group has been working on different cement grinding methods and processes, it has made in-depth research and comparison on technical requirements. It is said that the semi-final grinding process can effectively solve the problem of the current combined grinding phenomenon, and further improve grinding efficiency by using a roller press system with high efficiency. As many test results showed, it has a significant effect on reducing energy consumption. China United Cement Group has tried and tested the application of the semi-final grinding process since 2013, and it has proved to be effective.
Semi-final grinding process has shown advantages in cement grinding, and there are other tips for improving cement characteristics in production, as it is listed below:
Improve Cement Grinding Process For Better Cement Quality:
- Reasonable control of the proportion of finished products produced by the roller press system is the most appropriate. The specific surface area is more than 420m2 / kg, the accumulated amount of 0 ~ 32um is 97%, and the residual sieve residue of 45um is 0. The cement capacity performance is the best at this time.
- Control mining powder quality, blending raw materials, types and ratio.
- It is suggested that the cement production line includes the compatibility test of cement and concrete superplasticizer, and compare the correlation between cement composition, ratio table, particle distribution and cement performance.
Cement Ball Mill Control System
- Control the fineness of raw material. The fineness of feed material is 48% ~ 52%, and that of outlet material is 32% ~ 35%.
- Flowing Rate Control. The flow rate of materials in the cement ball mill is controlled, and the partition in the ball mill is forced to pass through the compartment; the discharge grate plate ventilation area is adjusted to select the use proper scheme, and the hollow part of the activation ring is blocked to adjust the material flow rate.
- Semi-final grinding needs fine management to achieve the best results, from the host selection, clinker, admixture, parameter determination and adjustment, control tools, and other continuous research and adjustment.
AGICO has been supplying new Cement Manufacturing Plant solutions and equipment for various sizes of Cement Manufacturing Plant, we can customize the cement mill types of equipment for each step of the cement production process, from raw material crushing, clinker production to cement grinding, packaging. If you are interested in starting a new Cement Manufacturing Plant, you can contact AGICO now!