How to Lower Heat Lost Rate in Cement Production Plant
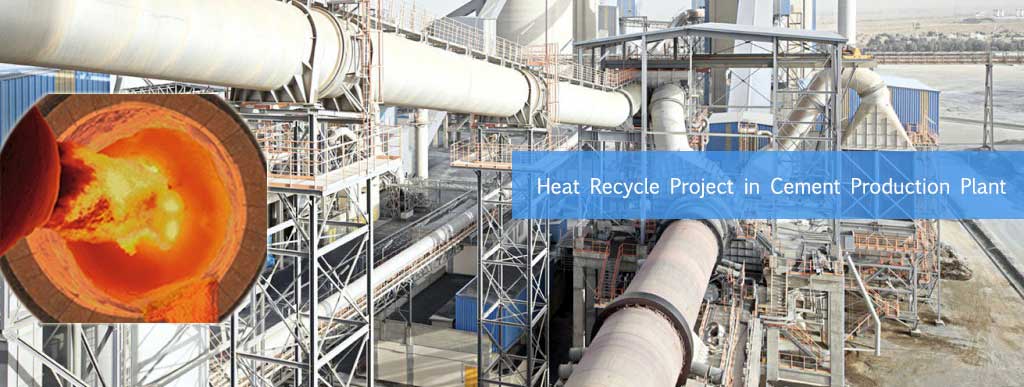
For most cement production plants, the surface temperature of cement rotary kiln shell is between 230 ~ 350 ℃, and the heat is dissipated into the environment by radiation and natural convection. Install arc set in the rotary kiln shell heat shields, with water as working medium, using the waste heat boiler waste water, skimpy share by the power supply of demineralized water treatment system, the circulating pump heat shields to set, the set of hot hot water temperature of 97 ~ 110 ℃, and feed water to heat exchanger of boiler at rotary kiln first, improves the thermal efficiency of waste heat power generation system, and then with water heat exchanger for bathhouse bath, and then add a pump, for production office district heating in the winter, after cooling water to go back to circulating water tank. The technology allows the investment in cement production plant to be recouped in the current year.
Cement Production Plant Upgrade Advantages:
In this cement production plant project, rotary kiln cylinder radiate heat recycling technology will kiln cylinder 360 ° closed, to a certain extent, recycling the tube on the surface of the body surface heat dissipation, but the way of recycling barrel and set gap heat shields the middle layer of air temperature in cylinder cooling impeded, the negative impact of calcining zone kiln tube in vitro table and inside of the brick temperature decreases, and rotary kiln's skin is easy to fall off. After removing the lower 180° heat collecting cover of the calcining belt, only the upper 180° heat collecting cover is retained, and the transition belt is fully closed at 360°. It has been 3 years since the operation after rectification without any adverse effect.
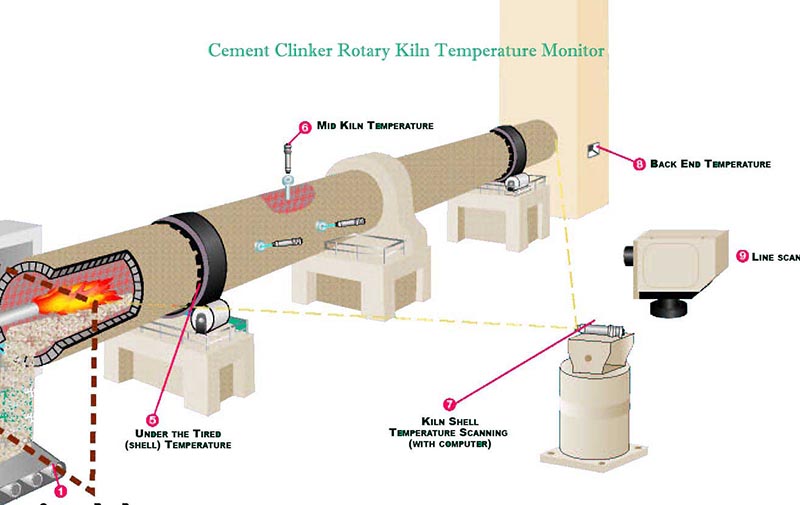
The original intention of the new practical technology design is to use heating, staff canteen, bathhouse heating water in winter, and bathhouse heating water in summer in the office area. However, the radiant heat recovery unit on the surface of the cement rotary kiln in this project has a heat production area of 375 m2. In practical application, it is known that the 30 ~ 35 ℃ water from the circulating pump is 30m2 per hour, and the water is supplied. After heating, the temperature rises to above 97 ℃, generating a lot of steam. In this case, with the bathhouse heating 30m2, the heat exchange tank can not absorb so much heat.
Tubular Heat Exchanger in Cement Production Plant
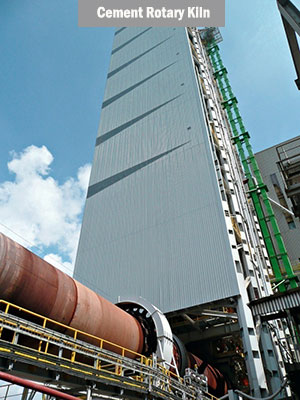
The water temperature of the backwater and circulating water tank rises. After re-entering the heat collection hood, the steam quantity is greater, and a large amount of evaporation occurs. Subsequently, a tubular heat exchanger was added. The first-stage tubular heat exchanger raised the water supply temperature of rotary kiln head boiler from 40 ℃ to 75 ℃, and the circulating water temperature decreased to about 75 ℃. The tap water is heated by a two-stage tubular heat exchanger. The circulating water temperature is reduced from 75 ℃ to 50 ℃, and the tap water is raised from about 10 ℃ to 50 ℃ for bathing and domestic use by factory workers. The 3-level heat exchange is the heating of the office building, central control building, some duty rooms, canteen and bathhouse in the production area. The circulating water temperature drops from 50 ℃ to 30 ~ 35 ℃, and then returns to the circulating water tank. Stop heating in summer, and tap water after heat exchange directly back to the circulation tank.
The cement production plant update application of this new type of practical technology to improve the efficiency of waste heat power generation, saving fuel for the purpose of heating, wash bath with hot water, expenditure on power, labor, annual maintenance, electricity, heating to reduce the coal burning boiler and heating coal dust and carbon emissions, save electricity, is the enterprise of cleaner production, the new method of energy conservation and environmental protection, low carbon life.
Cement Rotary Kiln Heat Recycle Feasibility
Although the excess heat was provided to the waste heat generation system, the cement rotary kiln shell accounted for 5.68% of the total heat dissipation, and the recovered radiant heat was very little. Moreover, since the calcium carbide slag in the raw material is treated by this rotary kiln, the calcium carbide slag content in the raw material reaches about 45%, and the outlet temperature of The C cylinder is kept at 350 ~ 400 ℃ for a long time. Compared with the waste heat of the exhaust gas, the radiant heat recovery of the rotary kiln cylinder has a negligible increase in power generation.
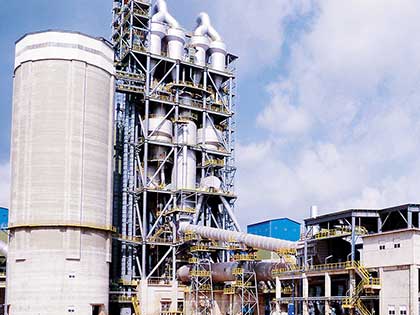
Why Use Heat Recovery Technology in Cement Production Plant
If we do not use the rotary kiln cylinder radiant heat waste heat recovery technology for heating and heating, but use other ways to achieve this heating and heating effect, our company spends about 1.3 million yuan a year. It can be seen that the total investment of this project is 1.495 million yuan. If the contribution to waste heat generation is added, the technology can recoup its investment in the current year.
Project | Material Cost ( Thousand RMB) | Manufacturing and Installation Cost ( Thousand RMB) | Civil Engineering ( Thousand RMB) | Total Cost ( Thousand RMB) |
---|---|---|---|---|
Steel | 500 | 300 | 800 | |
Equipment | 160 | 50 | 210 | |
Electrical Materials | 120 | 40 | 160 | |
Civil Engineering | 325 (including heating facility) | 325 | ||
Total Expense | 1495 |