Choosing Correct Feeding Machine Type For Cement Conveying System
Choosing the right feeding machine for a cement conveying system is crucial for efficient and effective material handling. The correct feeder can improve productivity, ensure consistent material flow, and reduce maintenance costs. Here AGICO CEMENT provides an overview of different types of feeding machines used in cement plants and offers guidance on selecting the appropriate type based on specific requirements.
Feeding Machine Types in Cement Conveying System
Plate Feeder | Screw Feeder | Disc Feeder | Impeller Feeder | Vibrating Feed Hopper | Vibrating Feeder |
(1) Plate Feeder
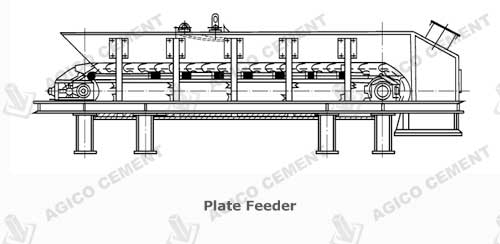
Plate feeders are mainly used for crusher feeding, and are divided into light, medium and heavy types. When the size of the crushed material is less than 200-300 mm, a light structure can be selected; when the maximum size is 350-450 mm, a medium structure should be selected; when the maximum size of the crushed material exceeds 450 mm, a heavy structure should be selected. Small cement plants generally only use light and medium structures. The schematic diagram of the plate feeder conveyor structure is shown in Picture
(2) Screw Feeder
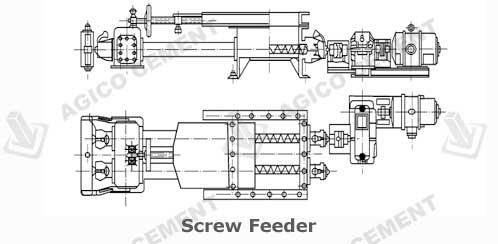
The screw feeder is suitable for uniform and continuous feeding of dry powder and granular materials. By adding pressure and flow stabilization technical measures or throttling measures, a steady flow screw feeder for quantitative feeding has emerged; by adding a weighing sensor to the volumetric method for steady flow and quantitative measurement to detect flow changes and automatically adjust the flow, a screw metering scale has emerged. The appearance of the SIW series double-tube screw feeder is shown in Picture.
(3) Disc Feeder
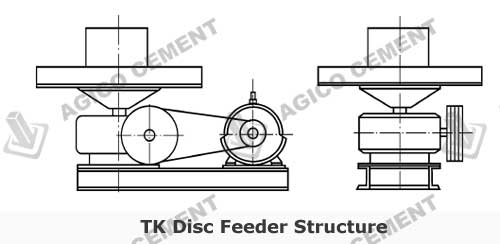
The disc feeder is a volumetric metering feeding device. When the particle size and water content of the material are stable, it can still be used by cement plants in underdeveloped areas. Many vertical kiln cement plants are still using it today. Disc feeders are divided into 2 categories: hanging type and seated type. According to the difference between the disc opening and closing, they are divided into open type and closed type. The appearance of the TK type disc feeder is shown picture below.
GF impeller feeder is a rotary disc feeding device suitable for volumetric measurement of powdered materials. Its working principle is that the powder is first scraped into the metering impeller of the next disc by the feeding impeller on the first disc, and then discharged at a fixed amount. The structural principle of GF impeller feeder is shown in picture. It is suitable for metering feeding of powders with good fluidity and low abrasiveness, such as coal particles and coal powder.
(4) Impeller Feeder
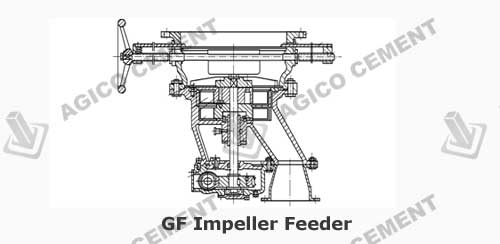
Impeller feeder is also called "grid wheel unloader". There are 2 structural types: elastic impeller and rigid impeller. The elastic impeller is a spring steel plate installed on the shaft, which rotates close to the inner wall of the rotary chamber, so the sealing performance is better. However, this impeller structure cannot rotate in the opposite direction, and this structure limits the speed of the impeller, which is not conducive to the production.The production capacity is small and the price is high. The particle size of the material in the cement plant is relatively large, so rigid impeller feeding is a good choice.
(5) Vibrating Feed Hopper
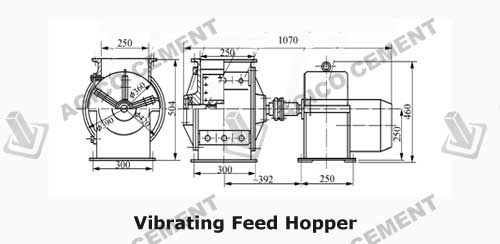
Vibrating feeder is a special equipment for breaking the arch and unloading various bulk material silos, and its application in cement plants is becoming more and more common. Vibrating feeder can be divided into 2 categories according to the type of exciter: one is the vibrating motor type vibrating feeder; the other is the electromagnetic vibration type. According to the force form generated by the vibrating feeder, there are five kinds of motion laws: vertical linear vibration, horizontal linear vibration, torsional vibration, flat rotation vibration, and vortex vibration. The vibrating hopper structure designed according to the principle of vibration is divided into single-mass and double-mass. At present, the most commonly used vibrating feeder in China is single-mass. The appearance of the GD series vibrating feeder is shown in picture
(6) Vibrating Feeder
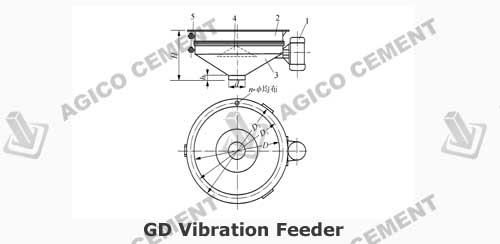
There are 2 types of vibrating feeders commonly used in cement plants: GZ series, derived electromagnetic vibrating feeders and vibrating motor vibrating feeders. The latter include DGZ series vibrating feeders and Y46 speed regulating vibrating feeders. GZ series electromagnetic vibrating feeders are a series of products that are supplemented and improved on the basis of DZ series. According to their structure and use, they are divided into 6 categories:
- The basic structural type is the bottom vibration type, which is used for feeding without special requirements.
- The upper vibration type, with the vibrator above the vibration trough, which is suitable for installation and use when the process layout space is insufficient. Others are basically the same.
- Closed type, suitable for conveying light materials with small bulk density.
- Light trough type, suitable for conveying light materials with small bulk density.
- Flat trough type, suitable for uniform feeding of thin material layers, especially suitable for the pre-feeding system of batching metering scales.
- Wide trough type, suitable for crushing and screening feeding systems with anti-impact measures.
GZ series electromagnetic vibrating feeder is widely used due to its small size, light weight, simple structure, easy installation and maintenance, low power consumption, and convenient flow adjustment. Under the condition of basically stable voltage, the feed amount can be adjusted with high metering accuracy. However, reasonable installation conditions and usage methods must be met. Generally, 6 factors should be concerned:
- Reasonably adjust the inclination angle of the vibration trough according to the material block particle size, water content, fluidity and other physical properties (generally 0-10 °, and a maximum of -15° for sticky materials).
- The angle between the feeder's suspension line and the vertical direction can be opened to about 10°, but should not be too large.
- The structure and shape of the feeding chute under the silo should avoid the silo pressure acting directly on the vibration trough. A pressure relief plate can be installed in the silo.
- The shape and size of the feeding chute, Generally, the side baffle of the chute is required to be close to the bottom of the trough ( b = 10 ~ 30mm), and the minimum distance a from the trough wall should be 20 ~ 50mm. The inclination angle of the rear wall of the chute α ≥ 45°.
- A spiral gate must be installed above the feeding chute for easy maintenance. The gate plate 8 for adjusting the flow is installed on the feeding chute 7.
- When using the electromagnetic vibrating feeder, the air gap between the iron core and the armature should be kept at about 2 mm (the design value of the GZ4 Measuring and Conveying 331 series vibrator).
Selecting the correct feeding machine type for your cement conveying system involves understanding the properties of the material, the required feed rate, and the specific conditions of your operation. By carefully considering these factors and the capabilities of various feeder types, you can optimize your cement plant's efficiency and performance. Proper maintenance and adjustments will further enhance the reliability and lifespan of the chosen feeding equipment, ensuring a smooth and continuous cement production process. If you are still have problem on choosing the feeding machine for cement plant, contact AGICO now for the professional advices!