How to Improve Working Efficiency of Ball Mill
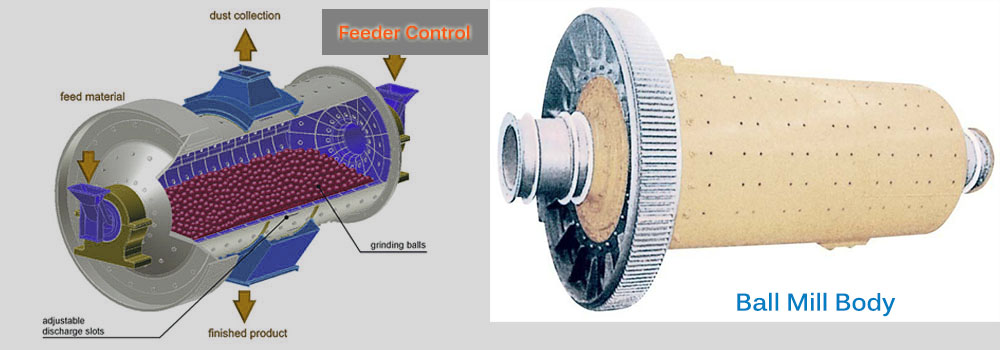
Control Feed Size
The particle size of the material entering the ball mill is controlled between 25-15 mm (the diameter of the ball mill is different for different feed sizes). Excessive rules will cause the ball mill to have too much fine material during the grinding process and cannot achieve the friction between the material and the material. Too thick will cause the steel ball to break the material for a long time, and will also increase the wear of the steel ball and the liner, and increase the maintenance cost of the mill.
Uniform Feeding
The feeding method of the ball mill is also very important to achieve uniform feeding. If the feeding is too small, there will be no material layer in the ball mill, and the steel ball will hit the steel ball and the steel ball will rub the steel ball, which will also cause waste of power resources. If too much feeding will cause the ball mill to rise, the rising belly will reduce the efficiency of the steel ball inside the ball mill, and the qualified materials can not be discharged, reducing the output. Therefore, it should be uniformly fed during the feeding process.
Improve Material of Liner and Effective Volume of Cylinder
Increasing the effective volume of the ball mill can increase the efficiency of the mill production. Ordinary alloy linings are thick and heavy, which reduces the effective volume of the mill and increases the power consumption, which reduces the production efficiency of the ball mill. Therefore, the material of the lining is very important. ZGMn13 (high manganese steel) lining is a suitable choice. The lining is reasonable in thickness and wearable. The surface hardness can reach HV500, which is equivalent to about HRC45. This can increase the wear resistance of the liner and increase the effective volume of the cylinder, thereby improving the working efficiency of the ball mill.
Control Fill Rate and Mill Speed
The processing capacity of the ball mill increases with the increase of the filling rate of the steel ball. Increasing the filling rate increases the probability of the ball grinding the ore and the self-grinding effect of the ore. The filling rate of the wet type lattice ball mill is generally 40-50%, the filling rate of the overflow type ball mill is generally 35-40%, and the filling rate of the dry type lattice type ball mill is generally 25-35%.
The speed of the mill will produce three ways of moving the ball:
- Centrifugal movement; when the cylinder rotation speed is increased to a certain limit value, that is, when the critical speed is reached or exceeded, all the medium will rotate with the cylinder without falling, which is called the centrifugal motion state of the medium. In the state of centrifugation, no grinding is generally produced.
- Falling state; the ball mill produces a throwing motion state when running at a higher speed, at which time the grinding process is dominated by impact crushing, followed by grinding. Ball mills generally work in this state of motion.
- The sloping state; the ball mill produces a sloping motion state at low speed operation, and the material is mainly pulverized by crushing and grinding action when the medium slides on each other.
Choose Right Steel Ball Ratio
According to the different grinding conditions, the proportion of the diameter of the steel ball is different. The diameter of the steel ball is generally divided into Φ120, Φ100, Φ80, Φ60, Φ40mm, etc. If there are many large materials inside the mill, then the choice is made. The proportion of the large diameter of the steel ball should be more. If there are many small pieces of material inside the mill, the smaller diameter should be more when selecting the steel ball. Because large diameter steel balls are mainly broken, small diameter steel balls are mainly used to grind materials.